The 7 requirements for agile factory operations
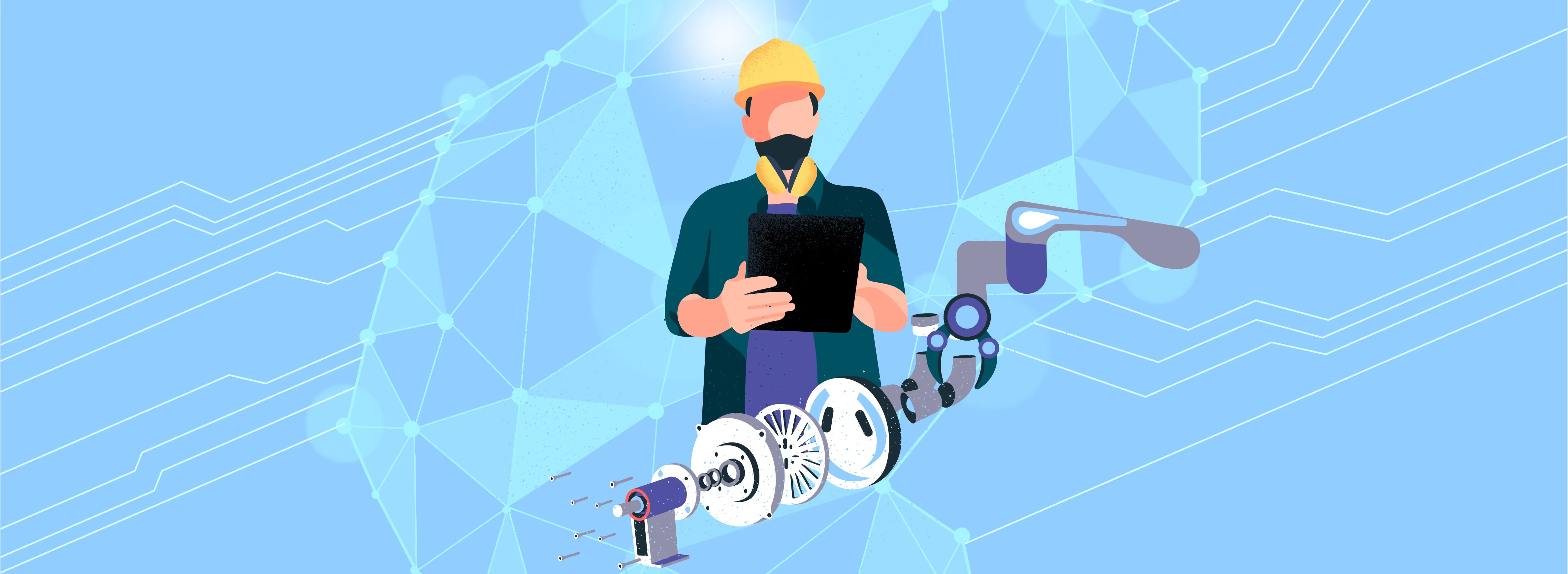
As companies look into the future, what can they do to ensure agile factory operations? Modern challenges require modern solutions. To streamline factory operations, we need new ways of mitigating uncertainty and establishing clear communication between teams, as well as consolidating data that provides the right people with the information they need to make quick strategic decisions under pressure.
Enabling real-time access to one source of truth
The first key requirement is to have one source of truth for operations data that provides a common language for different teams working on related tasks. This means no more Excel spreadsheets with data exported manually—instead, teams need real-time monitoring that’s instantly accessible, with all the contextual information necessary for decision-making. A holistic overview is essential, so links for all operations chain concepts—from purchase orders, customer orders and work orders, to quality notes and delivery events—are needed to give teams the information they need. Since each area of factory operations impacts another area, it’s critical that this data is translated into the right information for the relevant team. No more time-wasting and extensive cognitive labor: teams need instant access to accurate, clearly presented data.
Real time monitoring of future bottlenecks with algorithmic computations
Another requirement for agile factory operations is proactivity. This means anticipating future bottlenecks so that measures can be taken to adjust appropriately. It’s no longer enough to take a reactive approach. Manual calculations aren’t enough—algorithmic computation of future bottlenecks is needed, encompassing material coverage, and capacity of teams and machines at all levels of granularity, from work and service order, to production line, equipment family and plant. Turning these bottlenecks into actionable steps for each team will mean more time is spent actually dealing with the problem, rather than figuring out the solution that’s needed.
Continuous assessment of planning feasibility
Similarly, agile factory operations require the ability to quickly assess planning feasibility and impact of alternative plannings on north star metrics of the plant, including OTD, coverage rate, delay, revenue, inventory levels, turn around time, and WIP. When dealing with fast-moving situations resulting from supply chain constraints, factory managers will need to have an accurate overview of possible courses of action and their impact on key metrics. This will also facilitate quick decision making, as artificial intelligence solutions will be able to identify the insights and best next actions needed to optimize factory operations. One major benefit of technological solutions of this kind is simulation capabilities: manufacturers can use digital twins to assess the feasibility of alternative plans thanks to collaborative simulations.
Empowering teams to make quick decisions
In a fast-changing environment, teams need to be able to quickly identify the right decisions to take to avoid production disruptions. This can be achieved by enlisting the help of a powerful AI that can automatically identify the best course of action in any given situation, thereby optimizing operations planning. It should also be capable of assessing the feasibility of alternative plans (i.e. formulating digital twin scenarios) and simulate their impact on the entire factory plant operations, as well as on specific teams.
Streamlined collaboration across teams
Moreover, current ERPs are insufficient in terms of providing streamlined collaboration capabilities, since their scope doesn’t extend to emailing, messaging or other types of data. The result is endless email chains passing through various levels of upper management, whereas to work effectively staff needs to be able to collaborate across teams or receive instant notifications when stakeholders are needed on a problem or escalation ticket. They need to be able to easily find information related to ongoing corrective actions to answer a customer enquiring about the status of his order.
Powering digital transformation with UX-friendly interfaces
Moving onto the human element, reducing stress for teams is crucial in building solid and agile factory operations. As mentioned previously, ERPs are typically not intuitive nor user-friendly. Smart technological solutions with user-friendly interfaces, on the other hand, can attach objects to the issue with all relevant information—including purchase orders, quality notes, work orders, customer orders and part numbers—saving employees significant cognitive energy. Additionally, the ability to filter on a specific team comment to quickly assess status updates on a part of the value chain will mean teams are no longer left in the dark in terms of progress, and will better be able to make informed decisions.
Transparent data-driven leadership
The benefits of agile factory operations extend to leaders, too. Smart technological systems will need to enable smooth communication with executives on the status of operations, meaning leaders would be able to measure the gap between the Master Production Schedule and actual factory status. They would also be able to communicate this information to relevant stakeholders, and assess different alternative operations plans—and implement the optimal one—based on their impact on the factory north star metric.
.avif)
Agile factory operations are part of a larger tech stack environment. Needless to say, the scope of each solution as well as their interactions with one another should be well-defined for maximum efficiency.
.avif)
It’s a tall order, but successfully laying the foundation for agile factory operations will pay dividends for years to come. Investing time, money and effort into building agile processes will help mitigate risks caused by global uncertainty, reduce end customer dissatisfaction, and ensure employees are able to focus on their primary roles. Industry leaders of the future understand the necessity of these processes, and ensure steps are taken now to implement what’s needed to guarantee success in the coming years and beyond.