Digital Transformation: 5 Ways to Ensure Success
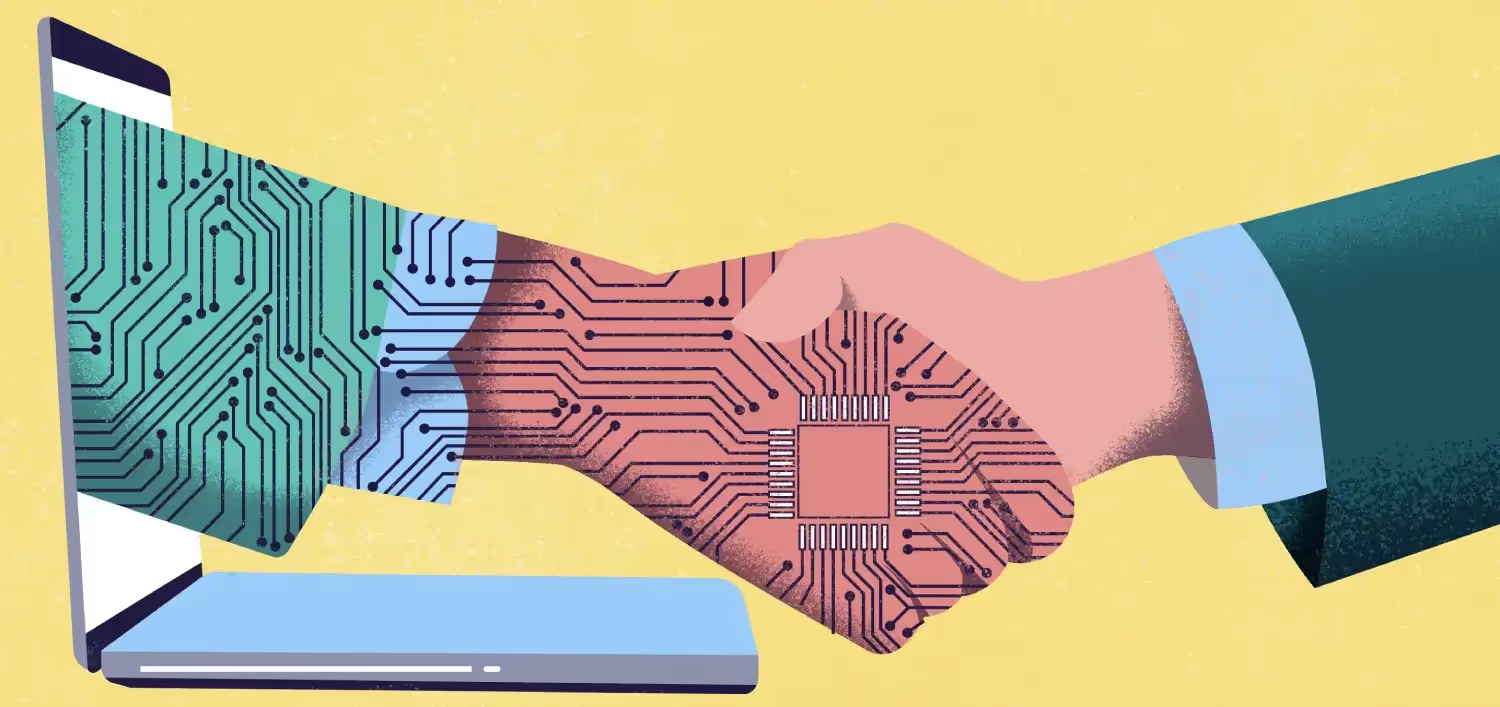
Last year, as manufacturing companies struggled to adjust to the pandemic, manufacturers were reminded of the need for digitalization if they want to survive and thrive in a world driven by continuous disruption.
So far, 2022 is continuing along the same lines, compelling digi-skeptics to flush their doubts down the drain. The challenges faced by operations managers — including geopolitical crises and international sanctions, soaring raw material prices, stricter environmental regulations and an overall increase in the standards demanded by customers — mean that adopting modern digital technologies is a matter of when, not if.
Indeed, the shock of COVID has accelerated the need for manufacturing companies to go digital. IBM’s “2021 Digital Transformation Assessment” finds that 67% of manufacturers have accelerated their digital projects as a result of the pandemic. Words like “efficiency” and “resiliency” are now at the top of their agenda.
Yet it is one thing to acknowledge the importance of digitalization, and something else to execute it successfully. According to a recent report by Deloitte, 70% of digital transformation projects fail and, even for those who succeed, it can be years even before they start delivering results.
The question that every manager should be asking themself is: how can I make sure that my digital transformation program belongs to the 30% that succeeds? How can you make the process efficient so not only shareholders, but also customers, see the results as quickly as possible?
5 ways to ensure the success of your digital transformation
1. Digital transformation must be business-led.
Digitizing is not only about gathering data — it is about connecting the dots. Most companies already have data flowing from almost every part of their manufacturing process, and many have invested huge amounts in creating data lakes and other foundational data projects waiting to find a way to reap the benefits of that information. How can this data be organized in a way that business users understand?
To achieve this goal, organisations and software vendors need to work with ‘ontologies’, representing the data and relationships relevant in the manufacturing and supply chain contexts. An ontology is a formal description of knowledge as a set of concepts within a domain and the relationships that hold between them.
An ontology allows users to get answers to their questions around concepts like customer, purchase and work orders, and, most importantly, understanding how they are interrelated. With ontologies, users do not need specific data science skills to be able to get the answers to help them in the daily operational decisions.
Having your data organized around business concepts and workflows allows taking optimum decisions that are aligned with the overall business strategy. In this way, data supports strategy execution, even at the level of micro-decisions.
2. Engage with users, not only management stakeholders.
We live in an era of collaboration. You never know where a solution or an important insight may lie, so top-down decision-making risks overlooking that issue that is making a process not work. Michael Hale, the author of WSJ bestseller The Digital Helix, claims that the number one barrier to thriving in the digital age is whether or not the people within an organization understand the challenges lying ahead. Successful digital transformations demand a shift in how people think, interact, collaborate and work, even if users have a hard time understanding this transformation.
We see this happen with Pelico users very often. Once they realize our platform helps them avoid a constant fire-fighting mode and reach their targets more efficiently, their initial reluctance stops being a barrier. When the “why” becomes clear, other elements fall into place.
3. Constantly align all 5 elements of the digital transformation.
When things do not go completely as planned, or the expected results are delayed (and there is a high probability that this will happen), go back to the digital transformation basics and ensure that all 5 components are in alignment: hardware, software, data, processes and people. At Pelico we pay special attention to aligning processes and people to ensure successful deployments and onboarding for our data platform.
4. Adapt to the urgency of the moment, prioritize accordingly and communicate your process.
Whether to go digital or not is no longer a choice anymore. It's not only technology companies that are thriving; other industries are also well ahead of manufacturers when it comes to digitizing their activities. In order to overcome this margin and get up to speed, manufacturing businesses should aptly prioritize their objectives, assessing the urgency and relevance of each action and communicating with the relevant stakeholders and teams in order to avoid inefficiencies and, most importantly, unmet expectations.
5. Research and educate yourself and your teams.
Digitizing your operations is not a one-time effort. If there is one thing to learn from high-profile digital transformations failures, that is to not get comfortable. The speed of technological development is lightning fast and it has been massively accelerated by the covid pandemic. For the success of the digital transformation, it is crucial to keep abreast of emerging digital technologies.
Nowadays there are thousands of companies dedicated to developing, testing and implementing solutions to problems that once had been thought unavoidable. Not surprisingly, nearly three quarters of manufacturing leaders (73%) say that promoting collaborations with start-ups is part of their long-term business strategy. The same survey, however, shows reluctance at doing so in the next 12 months, despite a huge majority of those having done so admitting they would gladly do it again. But if you want to thrive in an industry that is changing at giant steps, you better follow the example of the latter.
Go digital or go bust
As the World Economic Forum points out, the choice is clear: companies that are not able to go digital face significant risks of business continuity. But make no mistake—behind the technology, there is the need for people. If there is one thing that can hinder the success of a transformation process, that is management’s reluctance to change. To avoid that, we need a mentality change. The goal of a digital transformation is not just to survive, but to unlock new business opportunities and thrive in the future.
What do you see as the main success factors in the digital transformation of manufacturers?