How can companies in complex discrete manufacturing operate without shortages and improve their working capital?
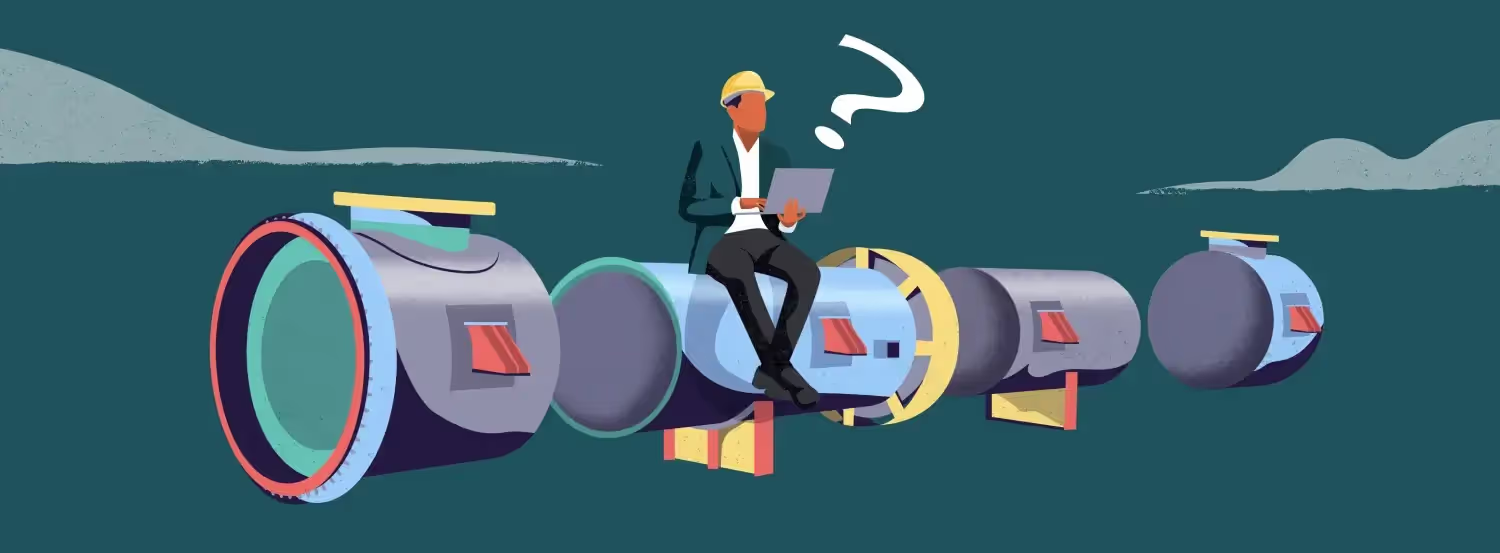
No roles within the manufacturing business have a more direct impact on efficiency than production controllers and supply chain managers. Their successes lead to smooth productivity, helping to fine-tune work-in-progress and, by extension, optimizing working capital. Their failures lead to shortages of parts that stall production, ultimately wasting capital, jeopardizing revenue and diminishing customer satisfaction.
Manufacturers must navigate a conflict: to improve working capital they need to minimize inventory in stock; but to operate without shortages, inventory reserves need to be kept plentiful.
Traditionally, companies have tried to tackle this puzzle with enterprise resource management software (ERP), with varying levels of success. In process manufacturing these tools can be sufficient: but for organizations operating in discrete manufacturing, producing complex products that require multiple sub-assemblies — the limitations of these tools quickly become apparent.
Why is this the case? In process manufacturing, production is formula focused. Parts are brought together according to a recipe, and they are simply combined. This is typically seen in pharmaceuticals, or in food and beverage production; industries that make products in bulk.
By contrast, discrete manufacturing is assembly focused. It requires precise, timely combinations of parts within specific sequences of sub-assemblies in multiple stages. We can think of industries like aerospace, automobiles, and smartphones. There can also be frequent changes to specifications from order-to-order which again add to the challenges.
Discrete manufacturers often implement made-to-order and made-to-stock production processes as well. Made-to-order, as the term implies, sees products manufactured to special or even individual customer requirements.
Made-to-stock is the strategy of making products in quantities based on projections about market demand. For some manufacturers, both strategies may co-exist, combining to complicate production.
Problems in supply
Production controllers often face challenges when parts become unavailable, leading to delays in the completion of customer orders. When it is discovered that a part is not available, teams need to first understand how to fix the issue. They then must find a different work order for the operator who was originally assigned to the unavailable component. And they also need to communicate with the client about the resulting delays.
This requires coordination and speed: the cumulative value of delayed orders over time can easily stretch into the millions of euros.
Manufacturing and supply chain operations have been increasing in complexity as a result of the growing complexity of products and organizations. A 2019 study found that, 76% of respondents reported dealing with three or more increased measures of complexity over the preceding five years — while 25% had seen their products become more complex in five or more ways.
This complexity has been made more difficult to tackle due to increases in the volatility experienced in supply chains, partly as a result of disruption to the globalized market. Greater complexity and volatility have started to demand more from workers, and yet many of them continue to rely on tools from the past.
The way it was…
In the past, when production teams at one aerospace manufacturer noticed a shortage, the resolution process would play out something like the following…
Day One
The operator discovers she has missing parts and notifies the Production Controller. The Production Controller then goes on the company’s enterprise resource planning tool, SAP, and checks the purchase orders. There, she discovers that there were some deliveries that had not been delivered on time.
The Production Controller then escalates the issue to the Supply Chain Manager, emailing him. But, like many busy professionals, the Supply Chain Manager regularly has 100 emails a day in his inbox — all of them urgent.
Consequently, nothing more is done that day.
Day Two
The next day, the Supply Chain Manager finally reads the email. He proceeds to analyze the stock at different plants, and even liaises with suppliers. They too use SAP to analyze the stock for each plant, further slowing resolution.
Potentially, Production Controllers could take stock from other plants in a bid to solve the shortage. But this could block another plant’s production instead, sowing deeply unhelpful internal tensions within the business.
Unsatisfactory results
Ultimately, for the business to operate effectively, decisions about how to resolve missing parts need to be made in 15 minutes. Despite the team’s best efforts, this approach to the analysis of data extracted from SAP simply cannot keep pace with the volatility and velocity of change. Missing parts could be spotted at 7am, but after the above resolution process takes place — two days might have passed.
As a result of this substantial inadequacy, there are constant waves of firefighting and crisis management hindering operations, leading to wasted capital and dissatisfied customers.
The way it is with Pelico
On time delivery is always the Production Controller’s primary goal. What they want is to achieve 100% adherence to the company’s master product schedule. But, in order to do this, they must bring delays in the resolution of missing parts down to zero.
In discrete manufacturing, with complex, multi-level bills-of-materials — this is only possible with a platform like Pelico. Schedule a discovery call to learn more.
Our technology absorbs complexity, aligns teams over a common view of operations, and empowers them to optimize daily decision making. And with Pelico, there is no need for pilots: the technology delivers value almost immediately.
Once the platform is up and running, any prediction of missing parts will result in an alert being pushed to the Production Controller. This is flexible, meaning time-windows can be adjusted according to the user’s needs. The alert itself contains a link to the Pelico 360° view with all contextual information about the production blockage. The Production Controller can then easily escalate the issue to the right person, who also receives a notification.
Collaboration with Pelico happens without emails or Excel sheets.
As with any new technology, there are certainly obstacles to adoption that must be overcome. IT access with every organization comes with its own individual challenges. Similarly, change management can put strain on teams, and these issues need to be monitored. Read another of our articles for insights into navigating digital transformation.
But after such hurdles are vaulted, the improvements in operational performance as a result of Pelico quickly become clear. For the aerospace manufacturer, this was evidenced by the speed up in resolution of delayed orders and noticeable improvements in the management of working capital.
To learn how Pelico could reduce delays and optimize working capital for your business, schedule a discovery call today.