On the march towards the digital plant
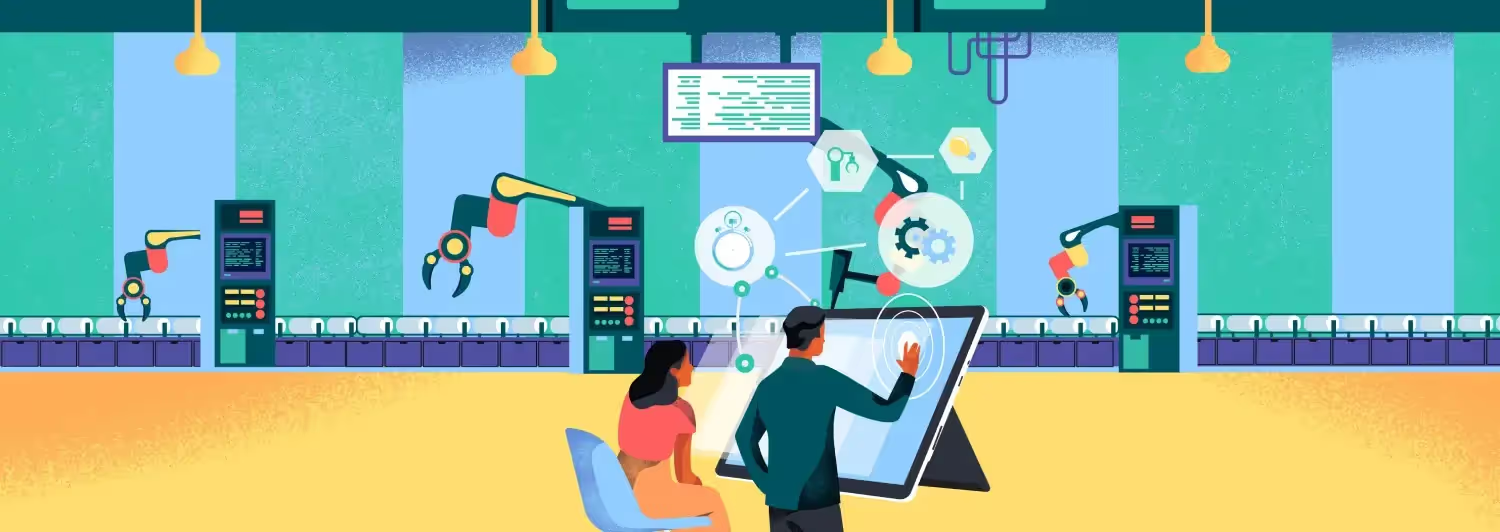
“Every business is a software business”, as technology pioneer Watts S. Humphrey famously said some two decades ago. Who would dare to challenge this claim today? Virtually all enterprises and industries are feeling the impact of the digital transformation that is reshaping our world.
Industrial production is no exception. 67% of manufacturers report that COVID-19 has accelerated their plans to adopt digital technologies. Successful digital transformation strategies can actually drive significant benefits for plants, as increased speed, agility and productivity drive efficiencies at scale and ultimately translated into improved revenue and market share.
However, on the flipside, it’s not uncommon to see industrial players struggling to figure out where to start, as digitalization involves recasting their time-tested business models.
This article outlines a 5-step path to help manufacturers unlock the benefits of digital transformation.
The Digitalization Imperative
Industrial manufacturers face unprecedented challenges, including a dramatic acceleration in product life cycle, increasingly strained resources, and the need to compete with new digital-native players (have you heard of 18-year-old Tesla? They became the most valuable car company worldwide during the first months of the pandemic, outperforming Toyota, Volkswagen, Daimler, and Honda combined). In this testing landscape, those firms that tackle the digitalization imperative heads on improve their odds of coming out winners.
The positive impact of digital and data technology for manufacturers cannot be understated. According to Gartner, 36% of manufacturing enterprises realize above-average business value from IT spending in digitalization. What more, 45% of respondents to an IndustryWeek survey indicate that IoT/Industry 4.0 technologies have enabled them to maximize output and maintain quality during the COVID-19 crisis.
For example, machine learning (algorithms that operate and learn based on lessons from existing information) helped General Electric increase production capacity up to 20% while lowering material consumption rates by 4%.
Long story short, intelligent digital technologies have the power to change the ball game radically. The performance gaps between those who got on board and the others is growing by the day. The march towards the digital plant is no longer optional.
Anatomy of the Digital Plant
The purpose of Operational Intelligence technologies is to help manufacturers speed up and improve both decision making and execution. How? By turning the plant’s data into an actionable production asset.
In the smart digital plant, data consolidation eliminates asymmetries of information to align all teams on the same goal - the one that maximizes the overall benefits and outcomes.
Artificial Intelligence (AI) leverages advanced analytics techniques to make sense out of events, extract predictive or prescriptive insights from both formatted and unformatted data, and automate or support decision-making. This way, everyone has a clear line of sight to the priority actions that will be most instrumental towards achieving that goal.
Process automation and real-time access to fresh, quality data are freeing up teams to focus their energies on higher added-value activities such as ongoing process optimization or innovation that’ll help improve customer experience and beat the competition.
This is already a reality. Operational Intelligence solutions such as Pelico’s are empowering manufacturing teams to cut through the fog of uncertain operations and achieve predictable outputs. So, what are the stragglers waiting for?
A 5-step approach to the digitalization of manufacturing
The thing is that digitalization can appear to be somewhat daunting to traditional manufacturers. Not only does it involve adopting new technology, but it also requires a cultural shift towards more agile mindsets, a new focus on individual and team empowerment, and some degree of willingness to embrace uncertainty.
Here’s a suggested step-by-step approach to help incumbent industrial players take the leap.
1/ Start with your strategic goals
Digital transformation is just another way to achieve your business goals. For this reason, you should never lose sight of the “because” of any digitalization initiative: the specific improvements and outcomes that you’re hoping to trigger through your technology investment. It is a good idea to start by focusing your effort on one of the key strategic goals set at the plant level (for example increasing planning adherence, reducing cost of missing parts & inventory, optimizing turnaround times, boosting productivity, etc.)
2/ Define a roadmap to your objectives
Once you know what your priorities are and what it is that you want to achieve, it’s time to identify the technology blocks that will take you there. At the core, Operations Management boils down to a data management problem. Big Data, AI & advanced analytics are providing a new path to address the long-standing problems of manufacturers — such as misalignments between Supply plans and production needs, constant shifts in demand, production blockers that could have been anticipated and avoided (e.g. missing parts, unavailable critical resources).
3/ On-board users with a concrete vision
Never forget that technology is nothing more than a tool and that value creation starts with usage. Granted, superior technology makes for superior tools, but the most important thing is how you use it. It is critical not to overlook the importance of change management: in order to engage your teams, you need to make sure they understand the rationale behind the initiative and that they’re supported in their discovery journey. Target users should be on-boarded from the get-go and should be part of the requirement mapping process (for example through POCs, pilot phases, prototypes, User Acceptance Testing, workshops, and more).
4/ Think big, start small
The importance of test-and-learn should not be underestimated. In modern IT environments, the cost of analysis is sometimes way superior to the cost of testing, as most tools can be deployed in a relatively short amount of time. This is why you should test the validity of your initial assumptions by deploying the new system on a limited scope, for example by testing it with a small group of highly-engaged users — ideally with an agile governance model — before making the required adjustments and committing to a broader roll out.
5/ Scale your success
Once you’ve put your ideas and assumptions to the test of reality, you can tell what works (and should be scaled or expanded) from what doesn’t (and should be killed). It is also a good idea to keep rolling out new functionality to address more business requirements, still following the same gradual, test-based approach.
All done? You’re ready to start thinking and operating like a truly digital company. Your bottom line will thank you for it.