Practical strategies for agility in a context of supply chain disruptions
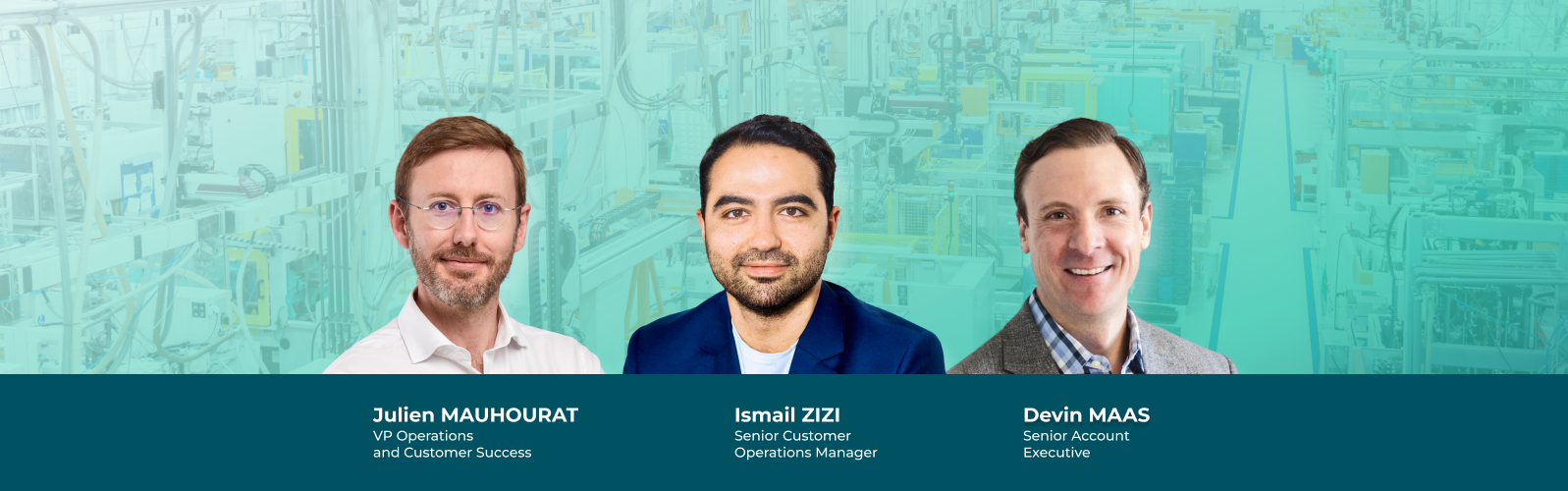
This blog post is the digest of Pelico's webinar on practical strategies for agility in a context of supply chain disruptions.
It will notably cover the 3 critical topics explored during this 40-minute session:
- How enhanced daily factory operations can help secure up to 10% of their revenue.
- 5 value stories of how industrial leaders increased supply chain resilience through an agile supply chain operations management platform in less than a quarter.
- Practical learnings from industry experts to secure competitive advantage through enhanced factory agility.
This webinar was originally hosted on April 21st, 2024, by:
- Devin Maas, Senior Account Executive with over 10 years of experience in the manufacturing industry,
- alongside Julien Mauhourat, VP of Operations & Customer Success and former McKinsey Associate Partner with in-depth expertise in Operations and Supply Chain,
- and Ismail Zizi, Senior Customer Operations Manager and specialist in the US market.
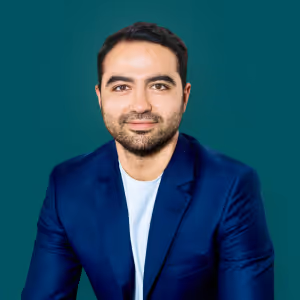
Senior Customer Operations Manager
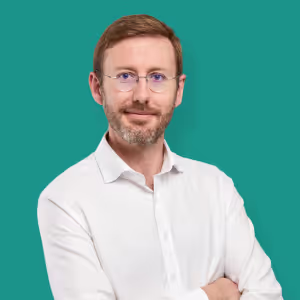
VP of Operations & Customer Success
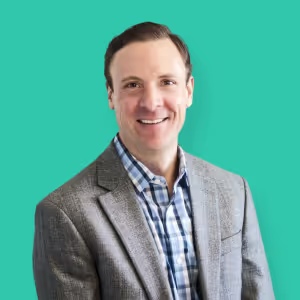
Senior Account
Executive
Note that this webinar was prepared based on Pelico's exclusive guide to the value of agility in the factory supply chain.
Focus on Agility
As a factory operations management specialist, Pelico is often confronted with industrial leaders who consider "agility" in the factory supply chain as another buzzword lacking substance.
As we'll refer to this term throughout the webinar, let's pause briefly to define and illustrate the concept and its levers.
How often do supply chain disruptions (really) happen in a factory
1 disruption occurs every 16 minutes, impacting 300K data points each time. Disruptions are a combination of shock and supply chain vulnerabilities. Shocks can be of different natures:
- External shocks —such as climate events or trade disputes.
- Internal shocks —such as labor availability or quality problems.
At Pelico, we have seen that these shocks are becoming more frequent and severe.

Factors for enhanced vulnerability toward supply chain shocks
Not all factories are born equal regarding vulnerability to factory supply chain disruptions.
According to McKinsey, supply chain disruptions will cost 45% of one year of EBITDA every 10 years. Of course, this figure can change depending on the supply chain type since some verticals are more exposed than others.
Here are the three main elements fostering increased vulnerability:
- Structurally longer supply chains, since they mean that a product has to travel across the world, and just one event in one place can have an impact.
- Larger bills of materials that involve many stakeholders, for which a single point of failure can impact the whole manufacturing process.
- Complex portfolios, with numerous SKUs calling for a more frequent portfolio refresh.
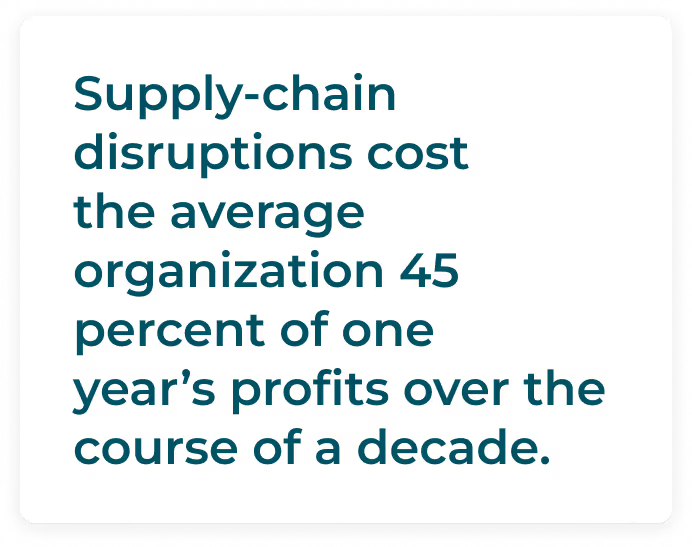
The Levers of Agility
Shocks will impact verticals differently, depending on the depth of the supply chain, the number of nodes, and the complexity of the BoM...
Traditionally, there are two ways to handle this:
- through the corporate supply chain strategy,
- or through enhancing your factory execution.
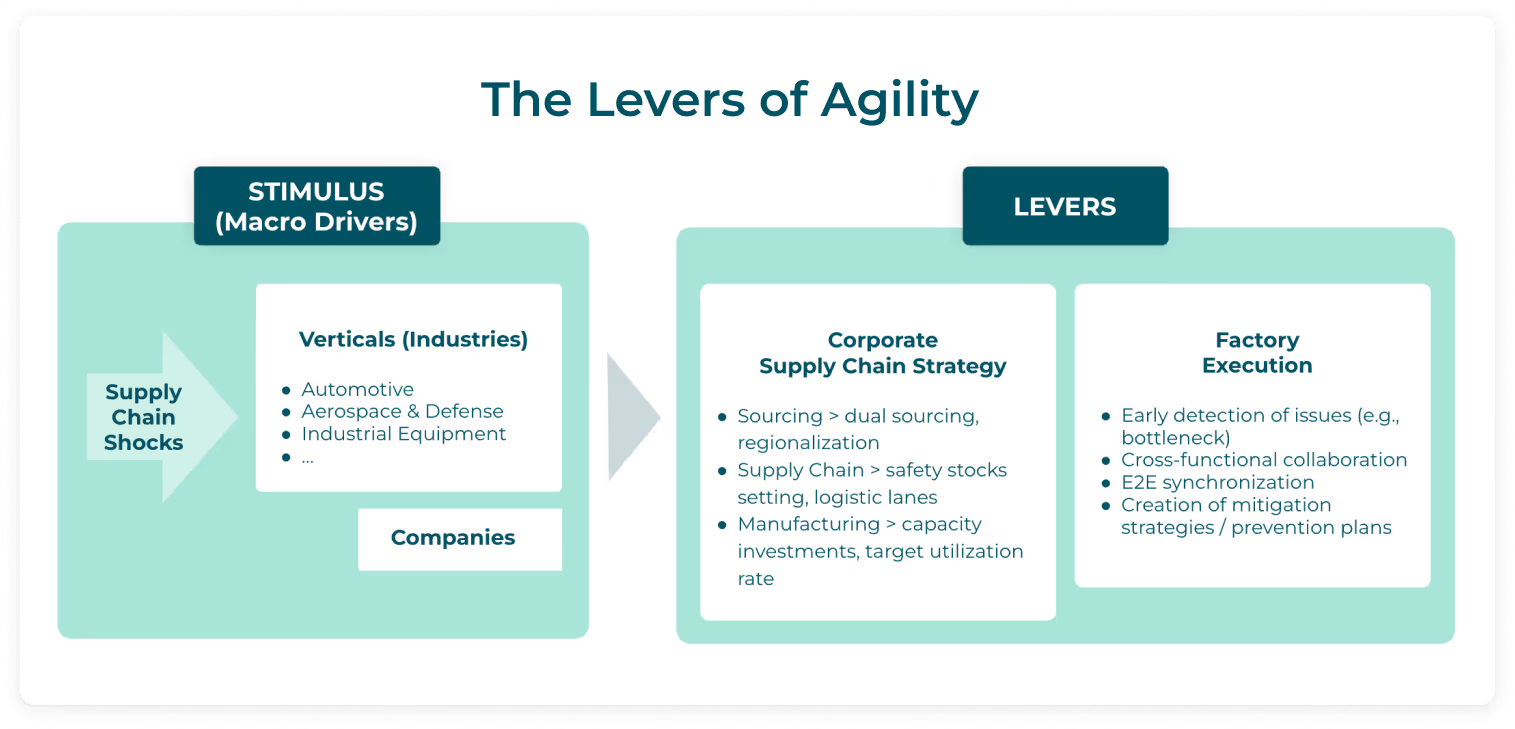
Corporate strategy
On the corporate strategy, you can notably use levers happening at the following levels:
- Sourcing: dual sourcing, regionalization...
- Supply Chain: safety stocks setting, logistic lanes...
- Manufacturing: capacity investments, target utilization rate...
Factory execution
On the factory execution side, you can also do many things. You can put in place early detection of issues or enable cross-functional collaboration. When facing a last-minute change, you must coordinate across multiple stakeholders inside and outside the factory.
That’s how you synchronize end-to-end your supply chain and create a mitigation strategy or prevention plan to respond. Both sides are essential.
Agility in a factory environment (how to be agile)
As introduced earlier, there are multiple ways to deal with supply chain disruptions at corporate and factory levels.
In that sense, agility is achieved by acting fast to all the different stimuli.
Buyers, production controllers, planners... We exchange with these level-one team members daily. This proximity, paired with our expertise, allowed us to identify five core pillars essential to gaining agility in the factory supply chain.
Alignment of all teams on a single source of data
There is no such thing as a factory where no suboptimal decisions are made. These poor decisions have a common denominator: they always come from data silos or blind spots, whether unadapted tools and or processes cause them.
This lever is about gearing teams with suitable methods and tools for easy access to exact and up-to-date data.
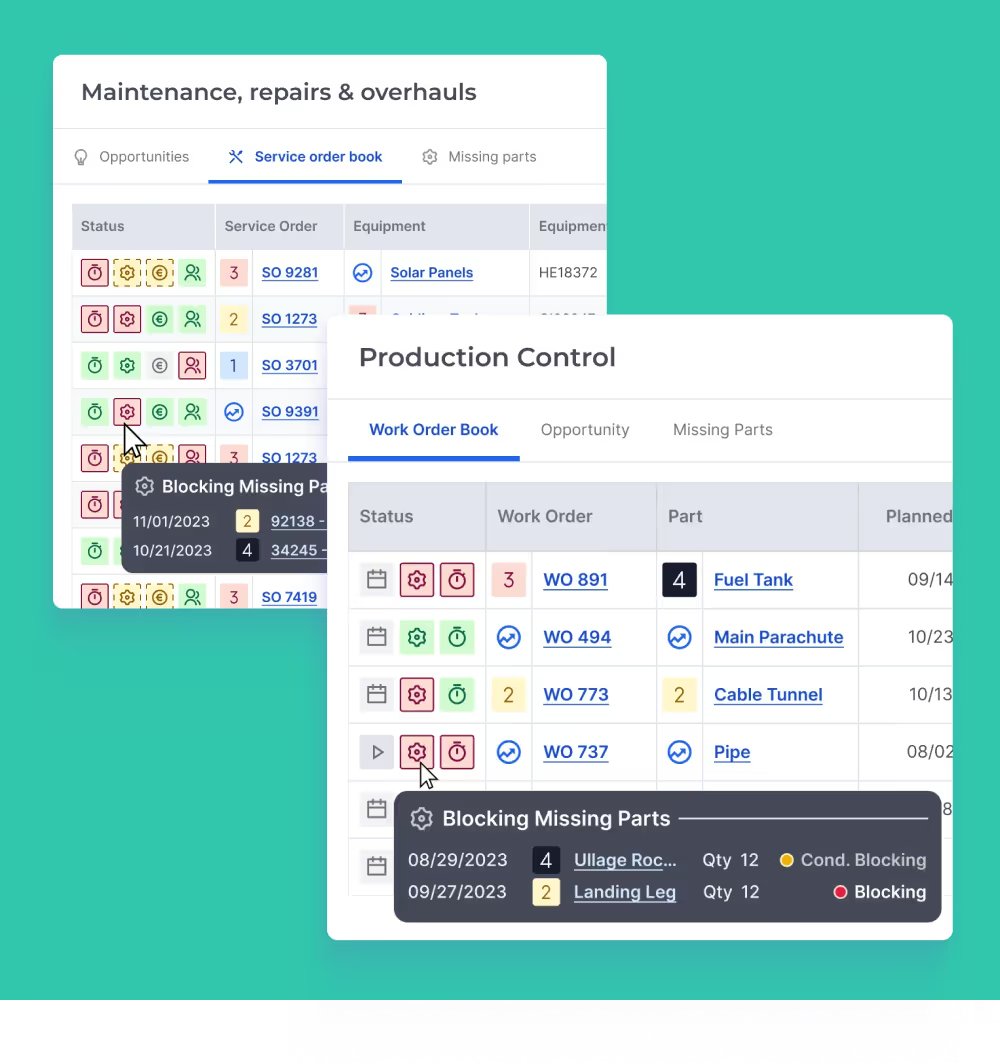
Early anticipation of bottlenecks
If you can anticipate a shortage earlier and detect its signals earlier, you will have more time to solve them.
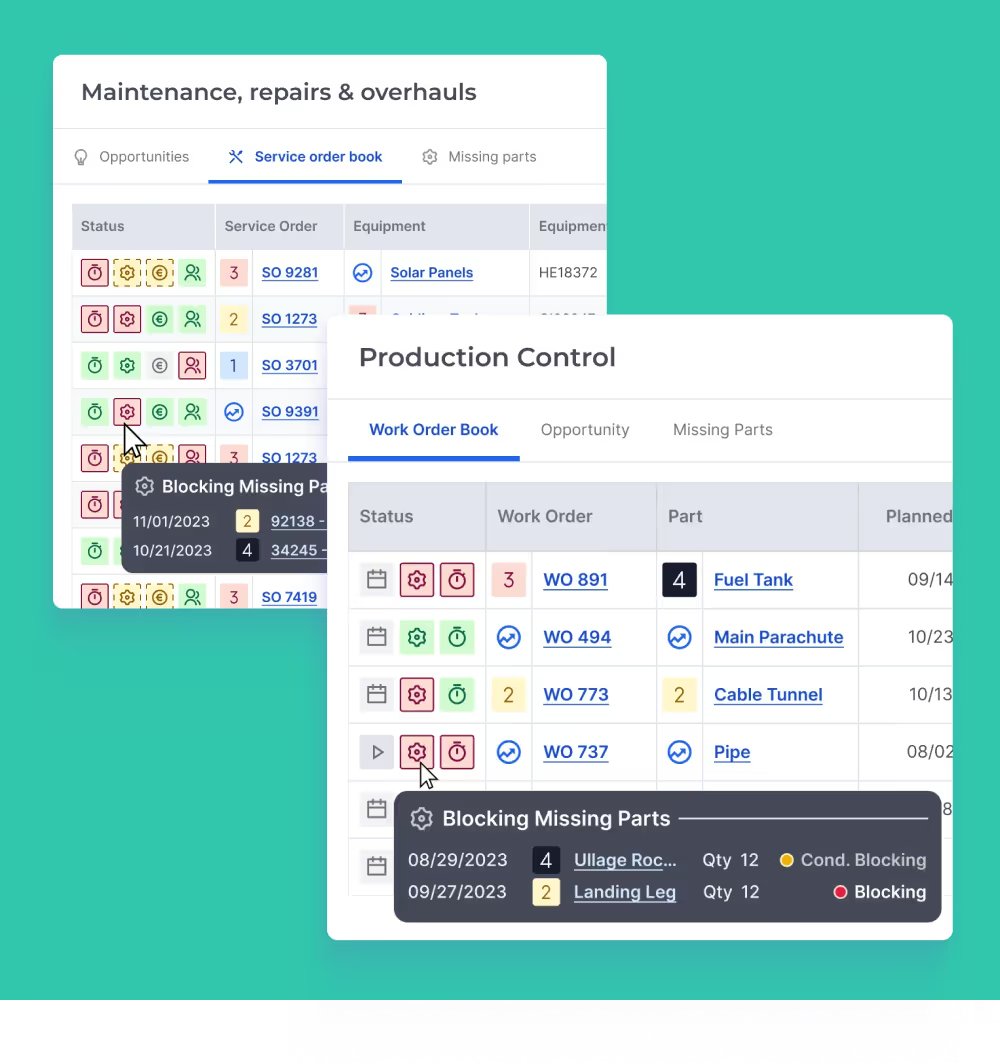
Quickly assess all possible decisions
When you can quickly assess all decisions that could be made to overcome this disruption and act fast on those, you're in an excellent place to help your factory to know a performance leap.
Far too often, factory teams struggle with having a full spectrum of potential decisions and finding ways to resolve those disruptions.
When a factory has a shortage, it could pull in its supplier but could also look at inspection stocks, rotable stocks, etc. With quick access to all those potential decisions, these decisions could be made on the spot.
Compounding these micro-decisions will make your supply chain operations (or execution) more agile.
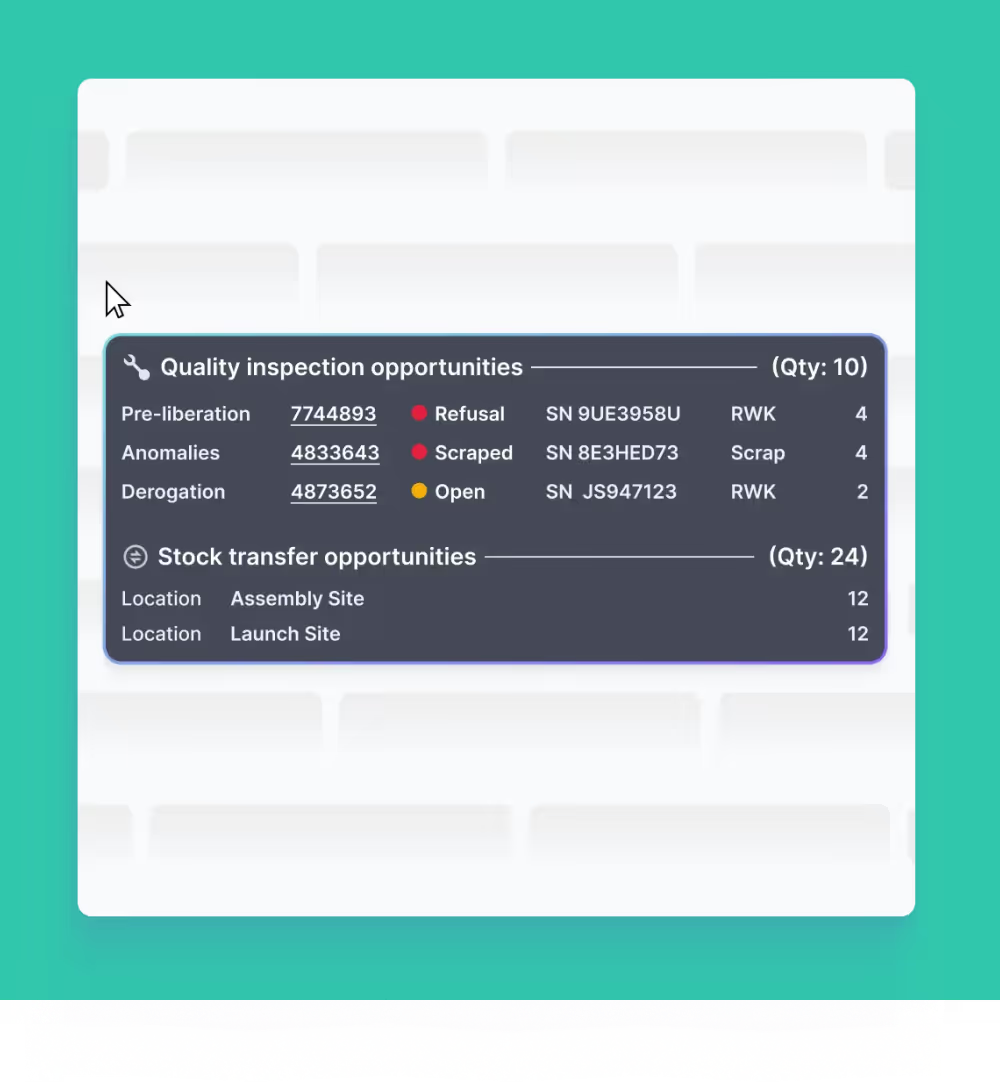
Streamlined cross-team collaboration
We often observe that factories tend to mix tools leveraging data and collaboration workflows. In a nutshell, this means a mix of emails, chats, calls, meetings, etc.
Our experience has demonstrated that embedding collaboration workflows within data software tools helps teams stay aligned, especially in more complex contexts.
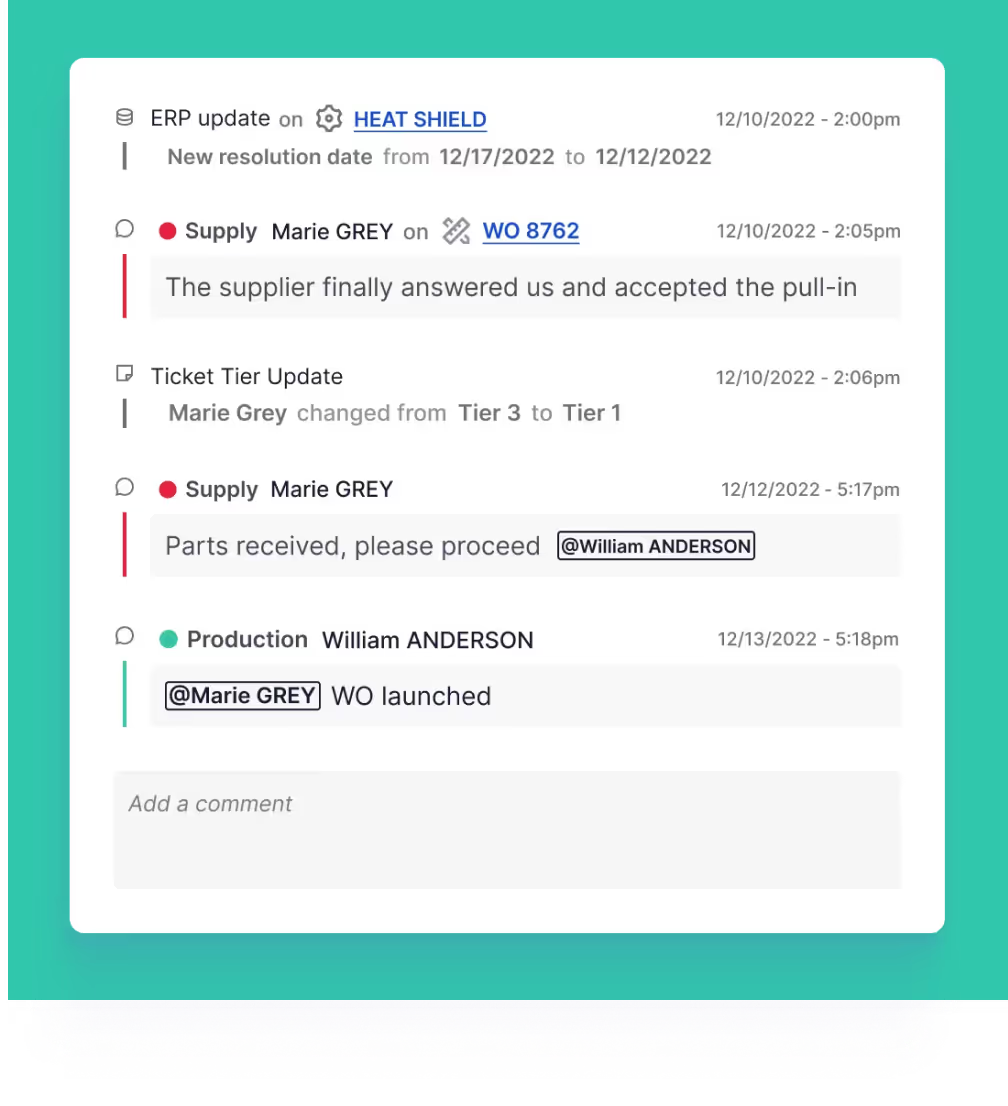
Simulate alternative scenarios quickly
Simulating alternative or what-if scenarios quickly is also an excellent lever for agility.
Once all decisions are made to overcome disruptions, they need to be assessed with regard to top-level KPIs.
To ensure that this execution is aligned with the corporate-level strategy, it typically needs to be done on the spot.
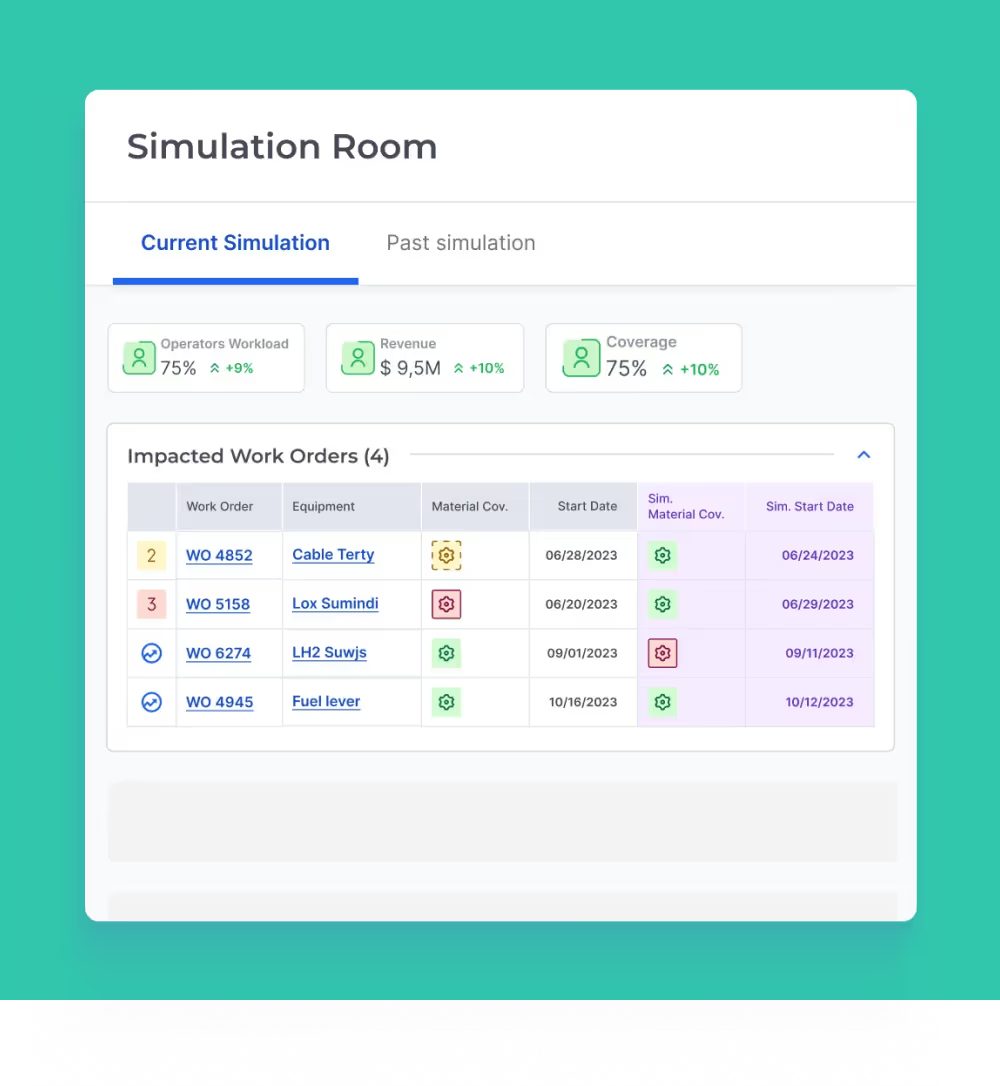
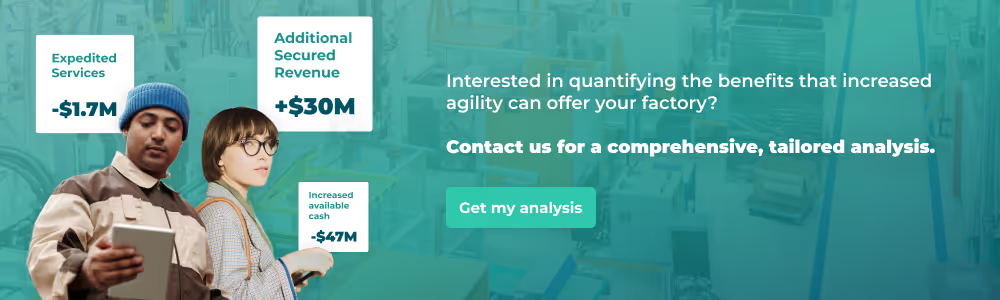
Quantifying Agility
The value of agility within the factory supply chain will vary based on the industry of your factory or group of factories.
Since we wanted to be more specific, we developed a methodology for measuring the impact of agility.
Methodology
The insights we'll share on the value of factory agility in the supply chain are based on data collected from our Aerospace & Defense industry customers.
We gathered data from dozens of factories using Pelico's platform over the past year. We then aggregated this self-reported data and computed the average value of each analyzed KPI, which we retrieved for a factory with $300 million in revenue — assuming all value KPIs are proportional to factory revenue. The charts and graphs included below display the figures of a factory with $300 million in revenue.
Please note that each graph's totals may not add up exactly, as we rounded values to the nearest tenth.
The value at stake
The impact of factory agility goes beyond cost. We can flag that impact across the different buckets. Here, we've framed these buckets as a P&L.
The P&L impact would be both on the top and bottom lines. You would affect inventory and services.
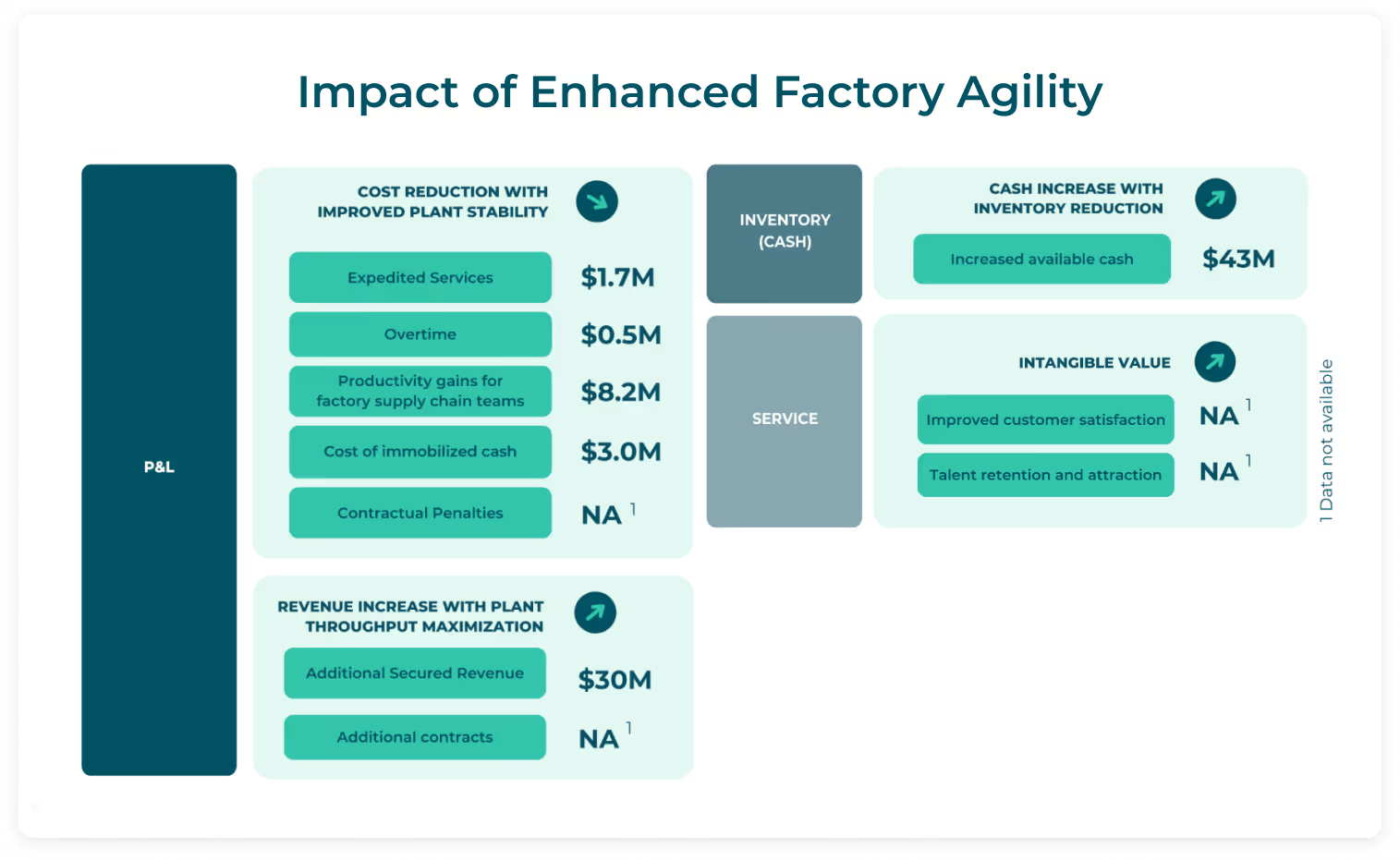
Cost reduction with improved factory stability
Let's take a look at the big buckets within cost reduction. We can see a gain in productivity from the factory supply chain team because you're wasting less time, you're more coordinated, you have fewer manual tasks to do or even fewer poor added-value tasks. Therefore, it allows you to reinvest your resource to extend your planning horizon.
You also see a $3M reduction in the cost of holding inventory.
Additional Secured Revenue
On the top line, we have seen the ability to secure additional revenue of up to 30 million versus the $300M revenue for our sample factory.
Intangible value
And then you have the intangible value, encompassing the increase in customer satisfaction, and retaining action on talents from factories. Indeed, when the factory moves away from an organizational pattern limiting poor added-value tasks, people can focus on what they really want to do, which means working on helping the supply chain perform.
How to unlock 10% of revenue from WIP reduction
Beyond savings, factory agility also allows to secure revenue from WIP reduction. With enhanced factory execution and enhanced factory agility, you can find a way to unlock some of this trapped revenue in the factory and ship it to the customer.
What we observe is that out of $150M of WIP for our sample factory with $300M revenue, a reduction of $30M directly translates into at least 10% of additional secured revenue over one year, which is quite significant.
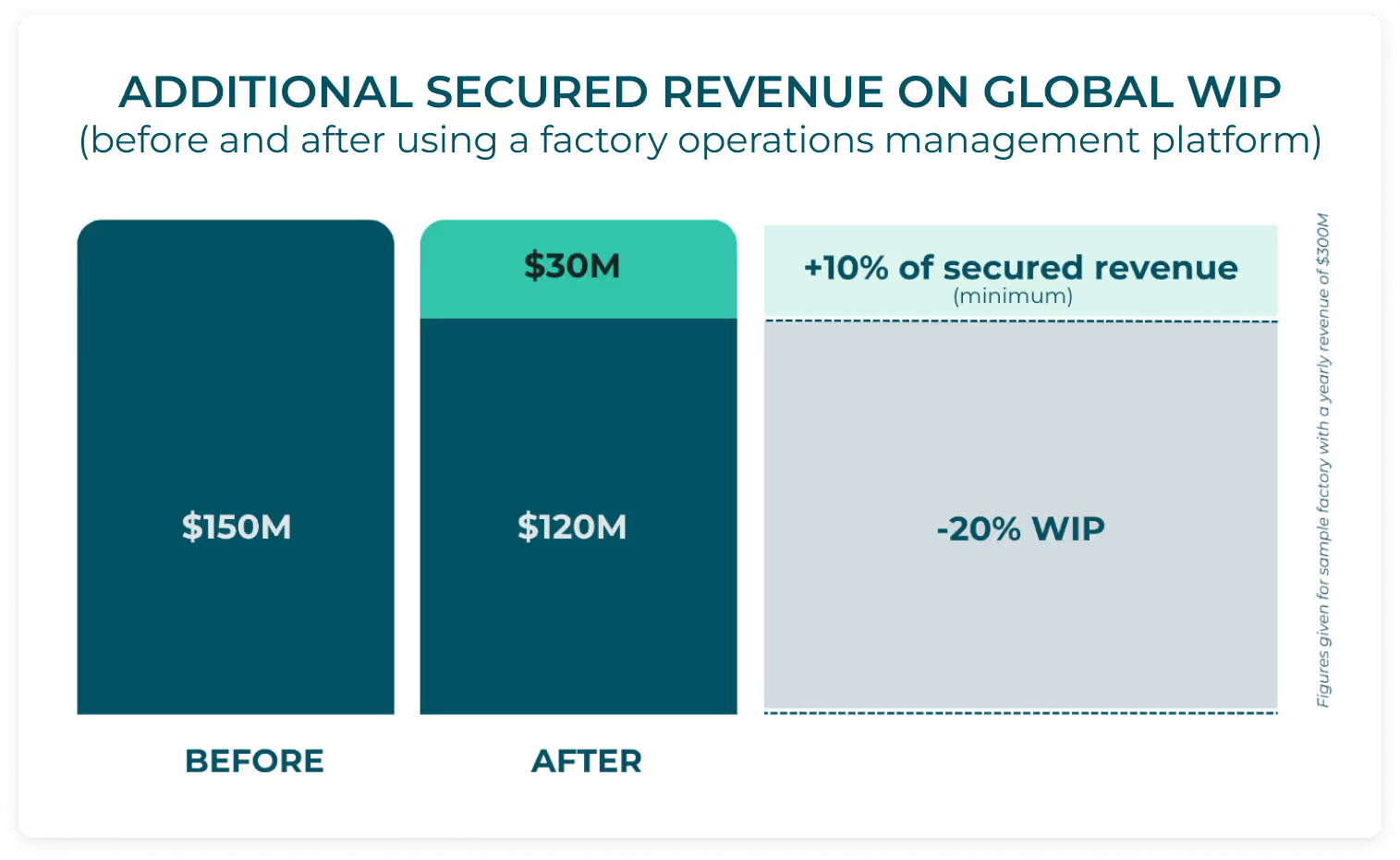
5 value stories on factory agility in the supply chain
Big Picture
The upcoming section will cover some real-life examples of how other industrial leaders are helping their operations become more resilient.
Pelico is trusted by various industrial players in multiple verticals of discrete manufacturing to solve their most critical challenges —aerospace, luxury, and industry equipment, to name a few.
As mentioned earlier, not all factories are born equal, leading them to embrace different strategies. Pelico's supply chain operations management platform is implemented and tailored, allowing our teams to ensure our platform supports factory objectives optimally.
5 value stories
Here are a few relevant value stories of how Pelico has helped different factories:
- Value story number 1:
WHO: A large aerospace OEM.
FACTORY OBJECTIVES: Avoid line stops on heavy projects through global multi-site collaboration.
- Value story number 2:
WHO: A luxury watchmaker.
FACTORY OBJECTIVES: Improve planning endurance and material coverage.
- Value story number 3:
WHO: MRO organization from the aerospace industry.
FACTORY OBJECTIVES: Reduce turnaround time and improve customer satisfaction.
- Value story number 4:
WHO: A leading Aerospace & Defense OEM.
FACTORY OBJECTIVES: Secure production ramp-up and improve clear-to-build rate.
ADDED COMPLEXITY FACTORS: Complex builds, and materials engineering are used to order materials, changing BOMs as they go into production.
- Value story number 5:
WHO: Aerospace and spare distribution
FACTORY OBJECTIVES: Increase customer satisfaction through enhanced visibility on end-to-end supply chain and estimated delivery dates.
How Pelico helps translate the factory's objectives into usage scenarios
As mentioned earlier, Pelico specializes in helping factories address their performance bottlenecks thanks to its unique capabilities and deployment methodology.
Pelico: a single platform to translate your factory's objectives into usage scenarios
At Pelico, we know that macroeconomic shocks impact verticals in different ways. Of course, these shocks will also likely apply to the corporate-level strategy of each of those groups within each vertical in different ways. Ultimately, this translates into what factories need to do, whether improving OTD, reducing inventory, improving coverage rates, reducing financial penalties, etc. Those corporate strategies impact factory operations.
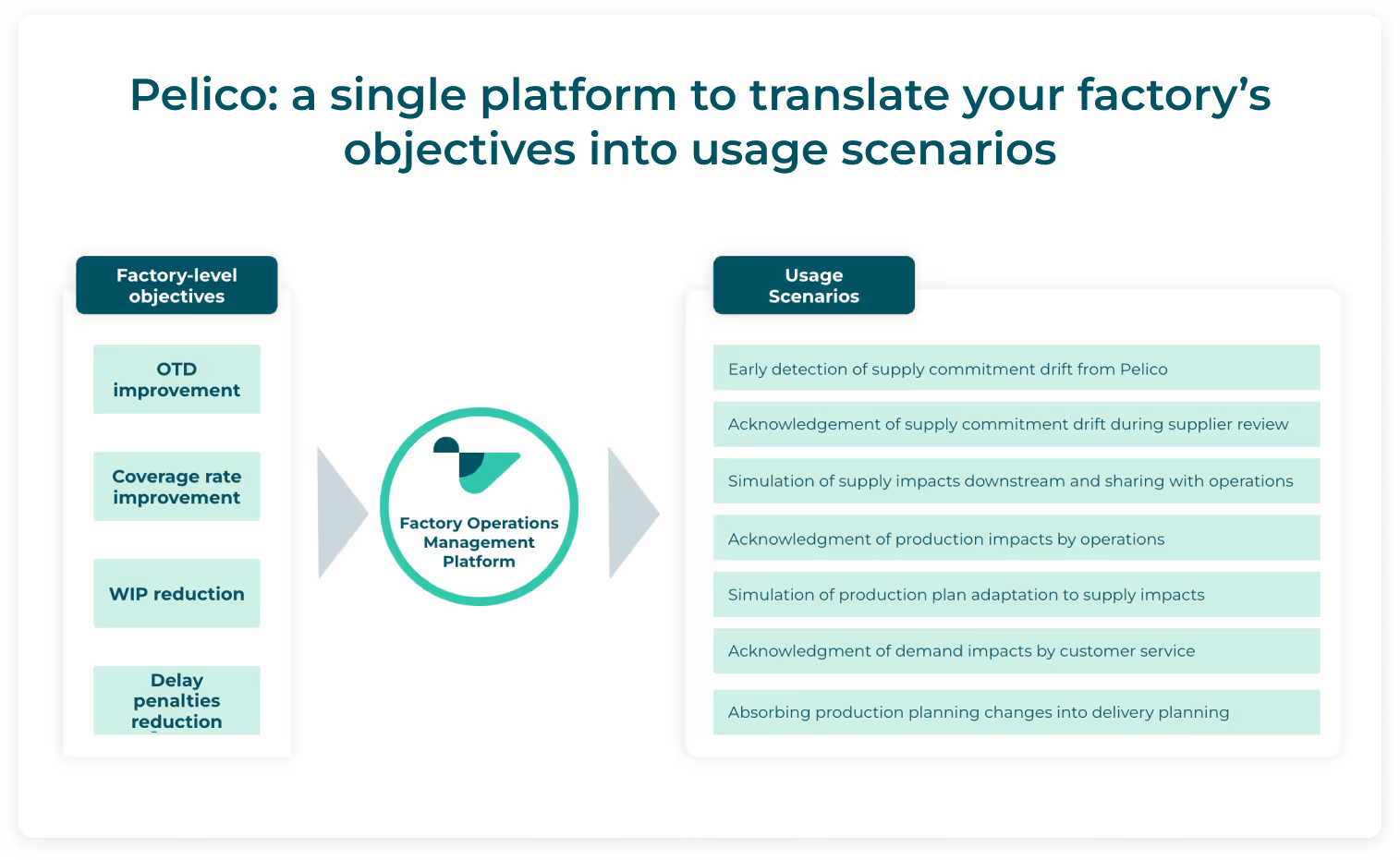
Pelico's goal is to directly link those factory-level KPIs with the custom usage scenarios we put in place within the teams, which are a mix of our features and the training plans we put in place with the teams.
Deep dives on the value stories
Let's deep dive into two different usage scenarios supported by Pelico:
- Absorbing supply disruption downstream for a large OEM Aerospace player.
- Reducing Turnaround Time and improving customer satisfaction in MRO.
Absorbing supply disruption downstream for a large OEM Aerospace player
This first detailed value story is about a factory struggling to improve its OTD, mainly through line stops. Due to its OTD problems, this factory ended up with a massive production backlog and faced delay penalties.
To help this factory resolve this situation, Pelico puts in place an end-to-end strategy with their supply, production control, and customer service teams to absorb supply change disruptions and translates that into better estimations for the end customer.
Reducing Turnaround Time and improving customer satisfaction in MRO
This second value story focuses on an MRO space organization seeking to reduce turnaround time dramatically.
To help this shop attain its objectives, Pelico's team implemented the following usage scenarios:
- Detect shortages within the MRO backlog early and give recommended actions on workaround solutions on those shortages to planners and kits managers.
- Reduce WIP with the same stock level just by reshuffling the repair plan.
- Assess the impacts of a customer prioritization campaign over a whole customer portfolio.
Practical Learnings on Factory Agility in the Supply Chain
Mitigate increasing disruptions with both strategic and execution levers
In a context in which supply chain disruptions happen once every 16 minutes, your plan becomes unsuitable very quickly. With strategy alone, forcing planning manufacturing won't give you enough resilience. It's essential to complement strategy with agile factory execution.
The value to capture with factory execution is high
Factory execution brings high value: it can represent a 10% revenue increase from the work in progress and $13M in savings.
More importantly, agile factory execution starts the virtual cycle, enabling factories to quit firefighter mode and enter planner mode.
Factories expanding their planning horizon are those unlocking the next step of performance.
Pair data and collaboration to rapidly enhance factory execution
The best MRP algorithm, ERP setup, or processes don't guarantee that your factory will be able to react very fast when facing supply chain disruptions, although they're a fact of life.
What will make the most significant difference between factories that succeed and the others is their ability to prioritize actions and align all teams very quickly—within the same day or the same week.
In that sense, factories should go beyond leveraging the data. They should embed data within collaboration and enrich it with simulation capabilities.
Final Thoughts
In an era marked by heightened geopolitical tensions, economic volatility, and the looming threat of global warming, the imperative for agility in factory operations is paramount.
To navigate these macro challenges, the modern factory must not only enhance its processes and tools for greater agility but also prioritize resource efficiency and embrace local production strategies.
This agility is crucial for factories to proactively anticipate and adapt to supply chain disruptions, guaranteeing uninterrupted and efficient production amidst the unpredictability of our times. If you're interested in making your factory more agile or curious to measure the value of agility for your own factory, contact us for a detailed analysis.
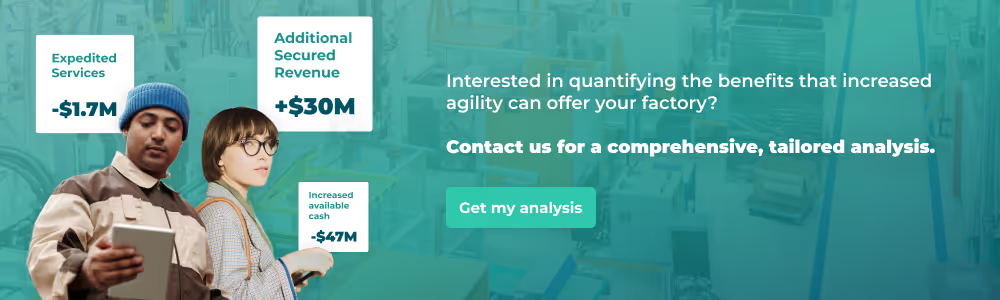