Continuously Adapting to Volatility in Supply Chain Planning
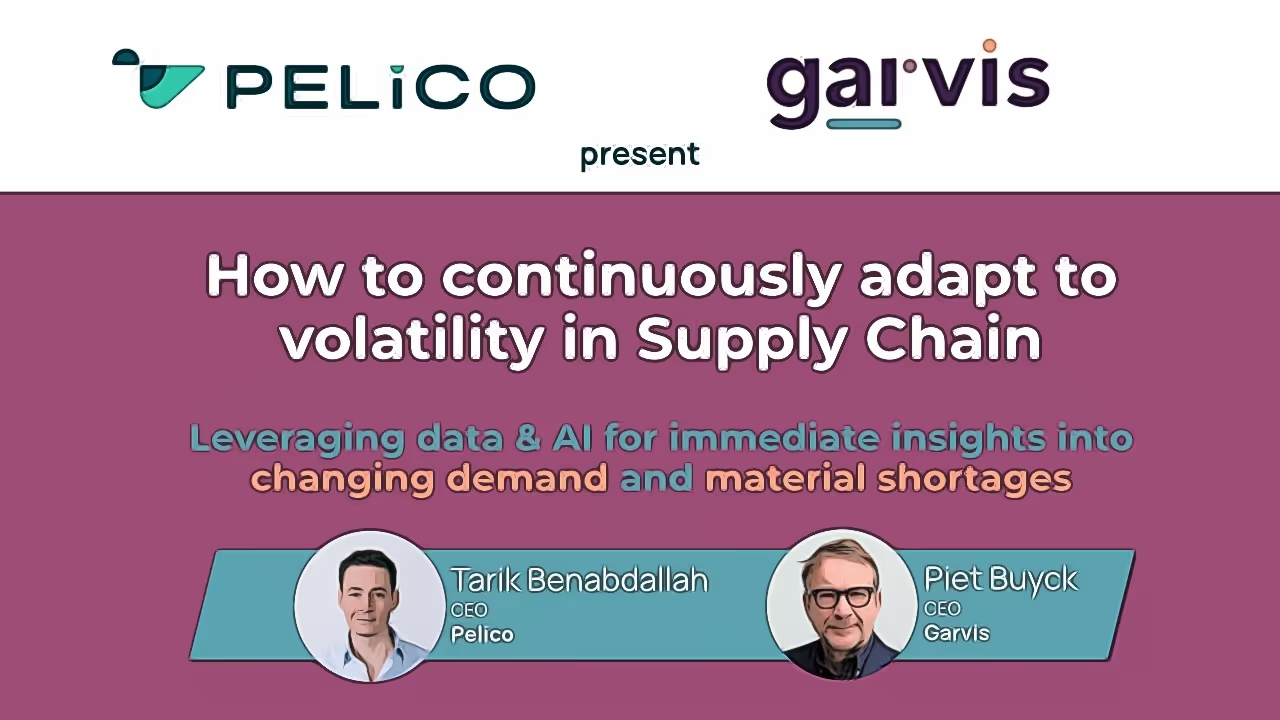
The Supply Chain industry is constantly evolving and companies are facing new challenges every day. The new reality of changing demand and unplanned material shortages are making Supply Chain planning especially challenging. In today's fast-paced and uncertain business environment, it's more important than ever to be able to adapt to volatility in the supply chain.
That's why we're excited to share with you a replay of our recent webinar on the topic of continuously adapting to volatility in the supply chain. Tarik Benabdallah, CEO of Pelico, co-hosted this webinar with Piet Buyck, CEO of Garvis.
Here are the key insights from this webinar:
The earlier and more accurately you understand changes in demand, the more accurately, faster and efficiently you can react to changes.
On the Supply Chain side, Work in Progress (WIP) context changes faster than teams’ ability to analyze and respond with current planning process. A lot of time is wasted on processing data and redundant internal email communication.
In order to react faster to the changes, and empower all the different teams to speak the common language and to coordinate in a more fluid way, traditional managerial routines for static situation with emails, excel simulation and lengthly internal meetings are not working anymore.
It leads to lengthy processes and conversations, and a lot of stress. Without the visibility early enough in those types of blockers, they don’t have the agility to act fast enough for blockers that may rise.
A continuous WIP monitoring at factory level becomes a requirement in today’s situation.
Pelico create a continuous feedback loop between what’s happening in operations and what happened in those process. It is a solution suitable for both manufacturing level and managerial level. With single source of data, it continuously
- monitors the feasibility of the weekly planning
- identifies the gap in material and capacity planning
- empowers teams to take actions at cranial level with AI-assisted recommendation
Two successful cases from Pelico:
- Pelico helped Collins Aerospace reduce cycle times and while increasing team productivity by over 30%
- Pelico helped Safran reduce 70% of parts shortages in 6 weeks
In the Q&A session, Tarik answered a few questions from the audience:
1. Are suppliers involved directly on the Pelico platform? Or just for internal stakeholders?
By default, Pelico can create value for internal stakeholders with available data at factory level.
When the customer has the access to stock level data of their suppliers, Pelico is able to leverage them into the platform as well to provide an extra level of visibility to the operational teams. But it’s not a requirement to make Pelico start adding value.
2. Examples on helping supply chain team like training for change management?
Pelico personalizes “routines” for each customer to simply empower the team by adapting with their existing working rituals and developing more features instead of creating a new way of thinking.
For each customer, Pelico empowers the team by creating a “routine” adopted with their existing working rituals.
More specific features can be developed along the way and trainings are provided for the team.
3. How does Pelico prioritize work orders and suggested actions? Can management define its own ladder in between products and customers?
Different companies have different operational strategies. Some care about delivering to customers on-time, some care about optimizing their sales, some care about reducing the amount of work orders.
To ensure all teams are working towards the same operational goal, based on the operational strategy, early in the onboarding stage, Pelico will define the goal at factory level with the customer. The goal will be configured in the product. Then we calculate the impact of bottlenecks towards this goal, and provide in-lined recommendation.
4. Is Pelico able to create master production schedules based on progress information? If yes, is it possible to integrate it with others like on Shopify platform?
No.
The role of Pelico is to leverage data from softwares like ERP that translate the customer demand into a master production schedule, to verify how robust the planning is, and to help optimize it.
5. How is Pelico different from other tools in the market? And highlight the salient different figures?
- Pelico connects all the stakeholders within the factory on a single platform.
- Pelico has embedded built-in operation expertise with operational algorithms to empower all the functions and align them over the critical path.
- Pelico is easy to deploy with 97% active user rate.
If you want to hear more details or life examples explained by Tarik, watch the full video.