How Safran Cabin Transformed MRO Operations and Boosted OTD
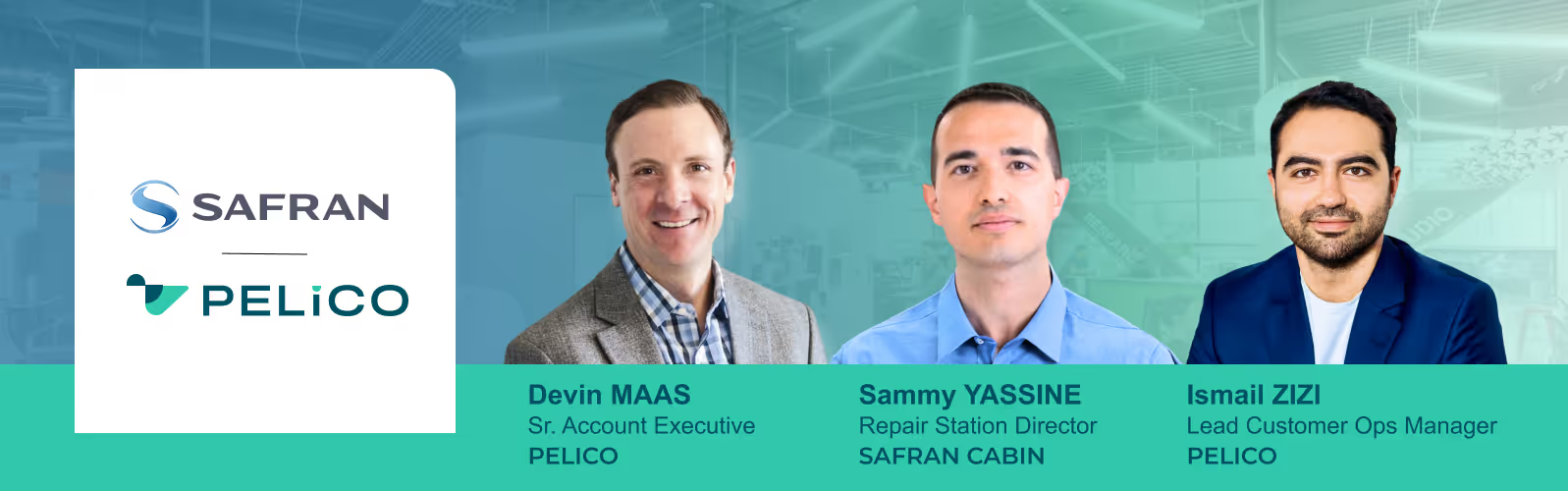
In a world where supply chain disruptions and increasing demands are the new norm, Maintenance, Repair, and Overhaul (MRO) operations face unprecedented challenges. Recently, Pelico hosted an insightful webinar, "MRO Shops' Digital Transformation: How Safran Cabin Enhances its OTD while Facing a Strong Ramp-Up," which shed light on how Safran Cabin has successfully navigated these challenges through strategic digital transformation. This blog post is a digest of the webinar originally held on June 13th, 2024.
Like the live session, this digest will cover three critical topics:
- How Digital Tools Can Empower Different Types of MRO Operations by Accommodating Their Specifics (Repair Order Complexity and Volume, Level of BOM, etc.).
- Pelico's Role in Supporting Safran Cabin MRO to Improve Its OTD by 8 Points by Enabling a Customer-Centric Approach and Decisions.
- How the Integration of a Supply Chain Operations Management Platform Supports an ERP Changeover Thanks to a Virtuous Data Loop.
Meet the Webinar Team
This webinar was hosted by:
- Sammy Yassine: Repair Station Director, Safran Cabin Garden Grove, CA, former Repair Station Manager with Safran Transmission System, and Safran Innovation Awards winner.
- Ismail Zizi: Customer Operations Lead and specialist in the US market.
- Devin Maas: Senior Account Executive with over 10 years of experience in the manufacturing industry.
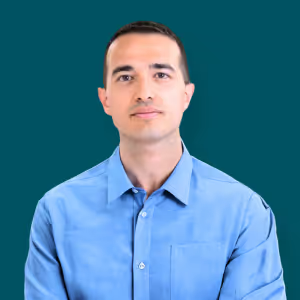
Repair Station Director
Safran Cabin
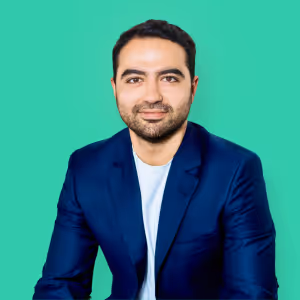
Customer Operations Lead
Pelico
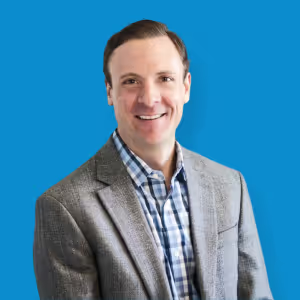
Senior Account Executive
Pelico
From Safran Transmission Systems France to Safran Cabin US: How Leveraging Data Improves MRO Shop Operations
From Safran Transmission Systems to Safran Cabin: Different MRO Shops, Different Stakes
Whether at Safran Transmission Systems (in France) or Safran Cabin (in the US), Sammy Yassine has embraced digitalization. For both sites, he implemented Pelico, winning a Safran Innovation Award in the process.
Here's a summary of the challenges encountered by these two sites:
- Safran Transmission Systems: Deals primarily with mid-mix, low-volume aircraft engines.
- Safran Cabin: Focuses on high-volume, complex interior assemblies.
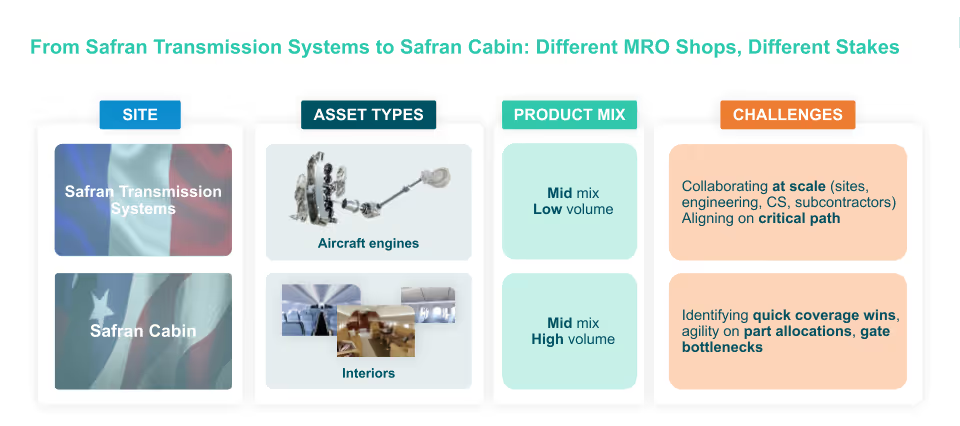
Safran Cabin is the second Safran site where Sammy Yassine implements Pelico. Back when he was MRO Production Planning & Supply Chain Manager at Safran Transmission Systems, he won a Safran Innovation Award with his team.
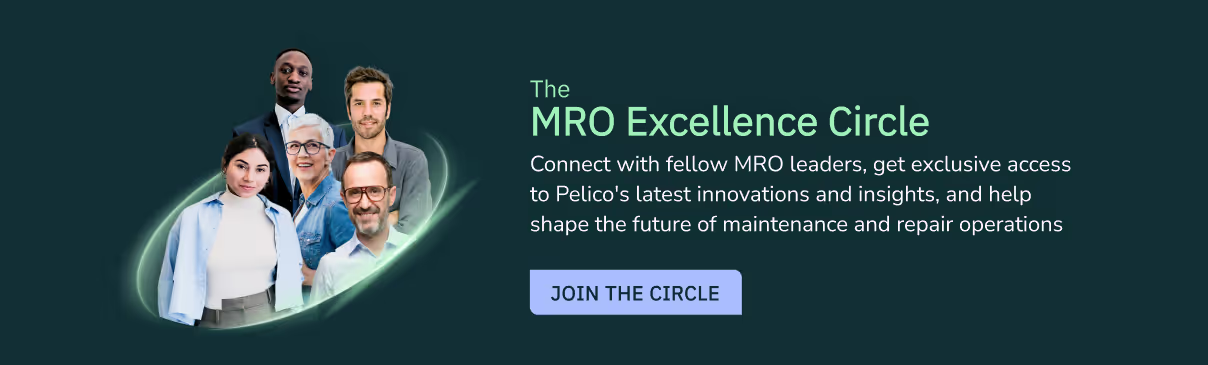
Safran
Cabin's MRO Specifics: Navigating Complex Assemblies and Strong Ramp-Up
"Safran Cabin faces a strong ramp-up while having an ambitious TAT goal of between 12 and 30 days," states Yassine. The shop serves 120 customers and runs maintenance operations for 600 different part numbers, representing 400 repair orders a month and mobilizing 5000 individual components. The main goal of this site is to improve OTD, which underlies higher customer satisfaction and many other elements.
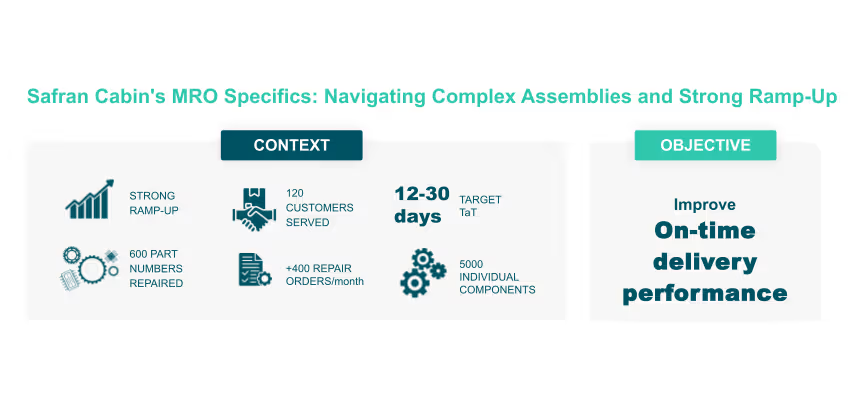
Safran Cabin MRO Challenges: Maintaining or Improving OTD Amidst Supply Chain Disruptions and Demand Ramp-Up
"We deal with two main factors at Safran Cabin," explains Sammy Yassine, "variability in the supply chain and in demand, both of which are crucial to our OTD performance."
- Supply Chain Variability: Disruptions demand significant resources to monitor, analyze, act, and ensure customers have clear visibility of the situation.
- Demand Variability and Ramp-Up: Repair demand changes daily, and post-COVID-19, they handle more repair orders than ever before.
To continue satisfying customers and remaining attractive, they need to work efficiently and continuously respond to these challenges.
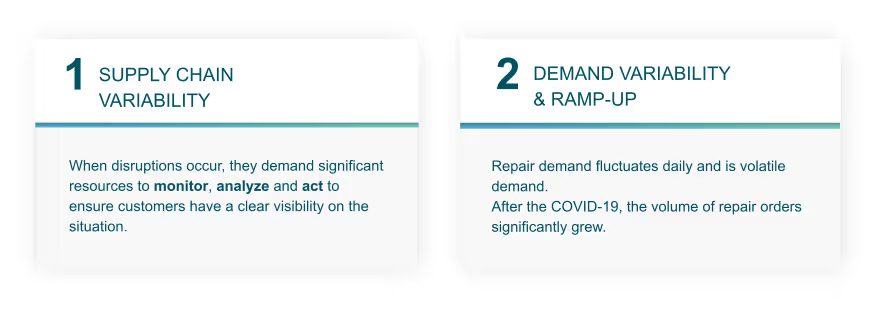
Pelico's Role in Supporting Safran Cabin MRO to Improve Its OTD
Safran Cabin MRO's Mitigation Strategy: Digitalization
Digitalization is part of our strategy.
- Sammy Yassine
"Digitalization is part of our strategy," summarizes Sammy Yassine. He elaborates: "MRO shops are brimming with data, both structured (like what's in Excel and ERP systems) and unstructured (like calls and emails)." Effectively using all this data is key to maximizing performance. Leveraging data to its full potential helps teams consistently make well-informed decisions.
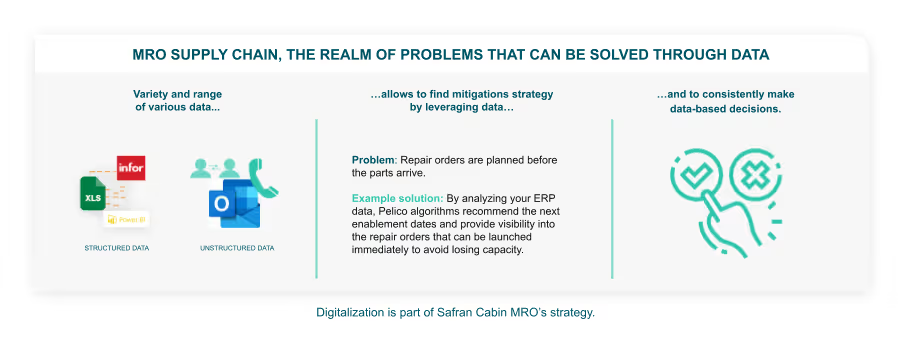
The Secret to Pelico's Positive Impact on OTD: An Intelligent Assistance Fueled by Algorithms to Identify the Critical Path
"Pelico's intelligent assistant uses algorithms to identify the critical path in supply chain operations," explains Ismail Zizi. "Pelico computes a wide range of data types throughout the repair journey, from the Material Reception Date to the Planned Start Date to the Delivery Date." Acting as a supply chain digital twin, Pelico connects the dots between different data sources like billing tools and ERPs. Pelico's algorithms, fed by this data, help teams with stock projection, pegging, lead time estimation, and simulation capabilities. You can read our blog on the Digital Twin concept if it's a topic of interest for you or your team.
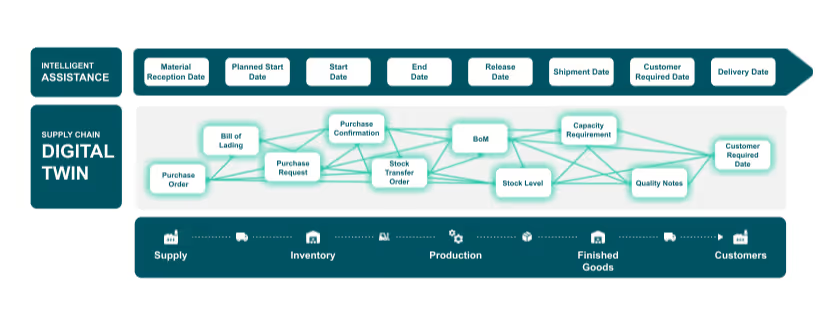
Pelico's Impact on Routine's Completion: From 90 Minutes to 15 Minutes
How many service orders can I release in reassembly? How many parts do I need to assemble?
"How many service orders can I release in reassembly? How many parts do I need to assemble?" are typically the questions that Safran Cabin MRO's team asks themselves.
Before Pelico, answering these questions took up to 1.5 hours because it required pulling data from Excel files, running M3 extracts, and multiple back-and-forth via emails.
With Pelico, the team uses an algorithm that suggests priority orders based on objectives like OTD and coverage, allowing them to make decisions rapidly (15 minutes).
This results in more time to secure longer planning horizons and enhanced bottleneck anticipation. Speaking of the devil, did you know that factories that are more agile tend to have wider planning horizons? If you’re interested in this topic, we recommend you read our dedicated guide on the value of factory agility in the supply chain.
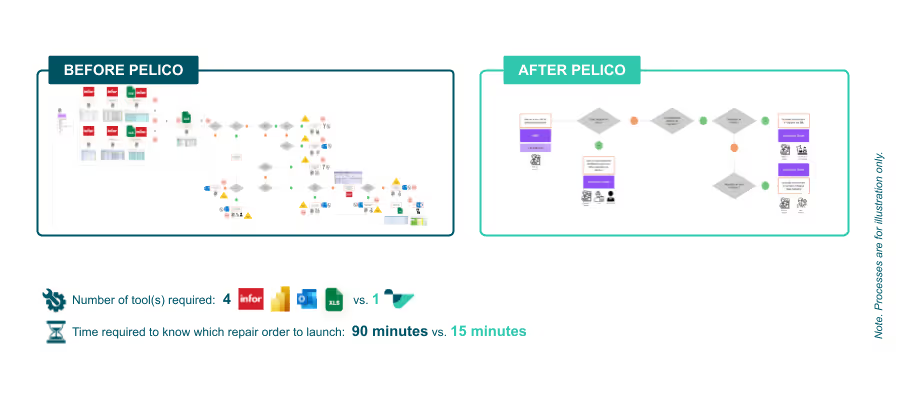
Pelico in Action with the Two Most Critical Usage Scenarios of Safran Cabin MRO
This section gathers the two live demos performed during the live session based on Safran Cabin MRO routines.
Push parts to re-assembly to optimize OTD
Secure the daily output by reallocating parts
How the Integration of a Shop Operations Management Platform Supports an ERP Changeover Thanks to a Virtuous Data Loop
Pelico vs. ERP - Positioning in the Supply Chain Stack
"Pelico’s operations management platform provides factory and shop teams the agility to manage their daily challenges. The platform aligns teams with actionable information and streamlines collaboration and simulation," underlines M. Zizi. He then continues with the difference and synergies between an ERP an Pelico: "An ERP, on the other hand, is more of a transactional system that centralizes data and ensures the consistency of business processes. The Pelico platform is fed by data from ERPs and other data sources. It organizes and processes this data to make it actionable."
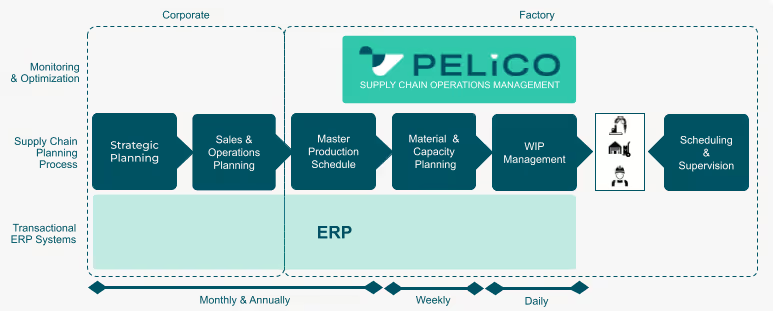
Strategic Timing: Integrating Pelico with ERP System Migration
We chose the third option: pairing the ERP migration with Pelico's implementation
- Sammy Yassine
"Initially, our shop identified two distinct needs that required different digital tools," remembers Sammy Yassine. Originally, we needed a newer version of their ERP (Infor M3) and a supply chain-specific tool to enhance performance. Because of this dual requirement, Safran Cabin had three options:
- Upgrade the ERP first, then implement Pelico;
- Start with Pelico, then upgrade the ERP;
- Do both simultaneously.
"We chose the third option: pairing the ERP migration with Pelico's implementation," summarizes the MRO. This approach, though challenging, has enabled my team and me to benefit from shared human resources, optimized interaction between the two systems, good momentum for tool adoption, a feedback loop for data quality and relevance, and one change management process.
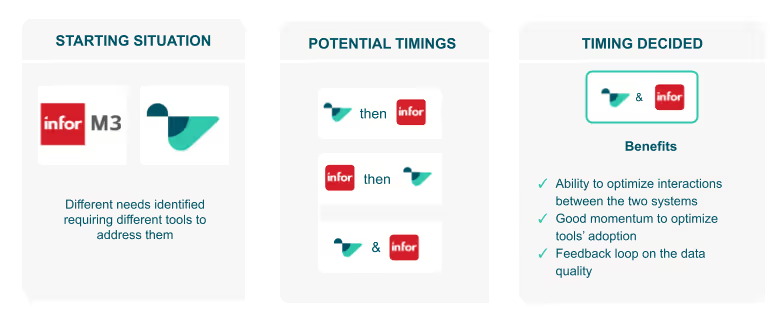
Safran Cabin's Winning Timing: Pairing an ERP with Pelico's Implementation
When asked about the positive impact of Pelico on its ERP migration, Sammy Yassine shares: "Pairing Infor M3 with Pelico has significantly enhanced data quality." He elaborates: "Pelico corrected thousands of data points and positively influenced how ERP migration needs were monitored. It also helped fully leverage ERP capabilities, notably with very specific pieces of information such as revised due dates or statuses."
Pairing Infor M3 with Pelico has significantly enhanced data quality.
- Sammy Yassine
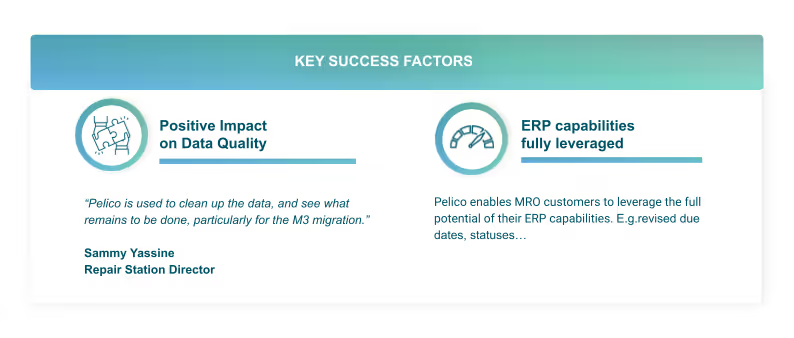
Safran Cabin MRO's Feedback on Pelico: Results
As the webinar ended, Sammy Yassine re-stated his goal: "Keep improving how we serve our customers." He then moved on to the "impressive" results obtained with Pelico. According to the MRO Director, Pelico delivers results in two ways:
- Customer-Centric Processes and Decisions:
- Maximizing Team Performance and Customer Satisfaction
Customer-Centric Processes and Decisions
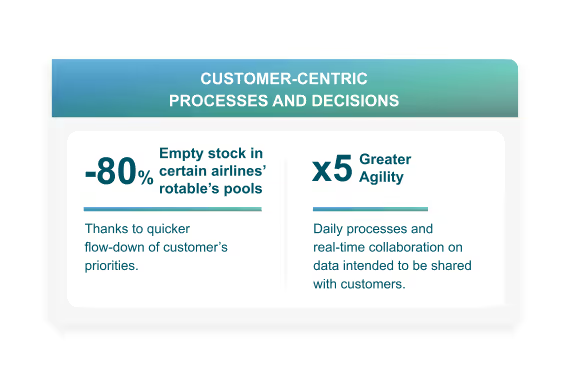
Two results are particularly striking, here: "we achieved a quicker flow-down of customer priorities, with up to 80% reduction in empty pool stock alerts with specific customers," says Sammy Yassine. He then moved on to the results obtained from switching to a daily process and real-time collaboration: "This approach has provided five times greater agility, but also helped making the data destined to be shared with customers (ship dates, status updates) continuously and automatically updated."
Maximizing Team Performance and Customer Satisfaction
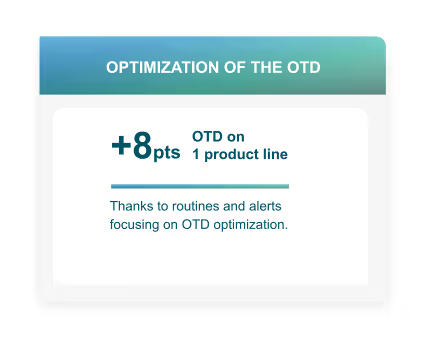
How about Pelico's impact on Safran Cabin MRO's OTD? According to the MRO, the results obtained rely on Pelico's ability to support routines: "Because the platform facilites routines and alerts focusing on OTD optimization, fast analysis, and decision-making, Pelico contributes to an 8-point increase in OTD on one product line".
Q&A
In this section, you'll find the summary of the questions and answers shared during the live session.
Was managing an ERP changeover alongside Pelico's implementation challenging? Would you recommend it to fellow site leaders?
Sammy Yassine: "These are two ambitious processes to conduct simultaneously. Each organization needs to consider its own situation. As far as I'm concerned, I've had the right resources and team, and benefitted from people with a great mindset to roll out ERP and Pelico together. It's not a universal answer, but it's doable."
How long does Pelico's implementation take?
Sammy Yassine: "In both the deployments I led, we saw results a few weeks after kick-off. In this specific deployment at Safran Cabin, we started seeing the first version of the tool and the first results six weeks after kick-off. We then kept building on that."
In both the deployments I led, we saw results a few weeks after kick-off.
- Sammy Yassine
Ismail Zizi: "Our focus is to bring value to the team incrementally. We try to unlock the value usage scenario by usage scenario. With Sammy's team, we started by working on releasing a consistent number of repair orders daily. This value creation indeed took about four to six weeks."
Can Pelico assist its users with data cleaning, and if so, how?
Ismail Zizi: "We get this question a lot. It's a common challenge for leaders. Implementing a tool on top of their ERP can be intimidating. ERP systems are like drawer systems; some drawers are organized, and others are messy. Pelico favors data cleaning by providing instant visibility on data that needs cleaning. For example, if you have purchase orders with past due dates, Pelico will make them visible instantly. Additionally, having several teams sharing the same tool and data creates a reinforcing loop where people ask their peers to clean data."
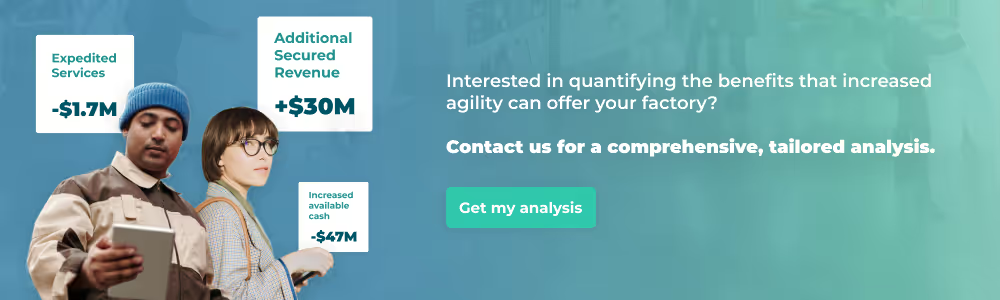
To Go Further
Please visit our MRO page for more detailed insights on how Pelico can help your MRO operations.
Have a question? Drop us an email, and we'll get back to you shortly.