ERP exception messages flooding? Here's how not to be overwhelmed
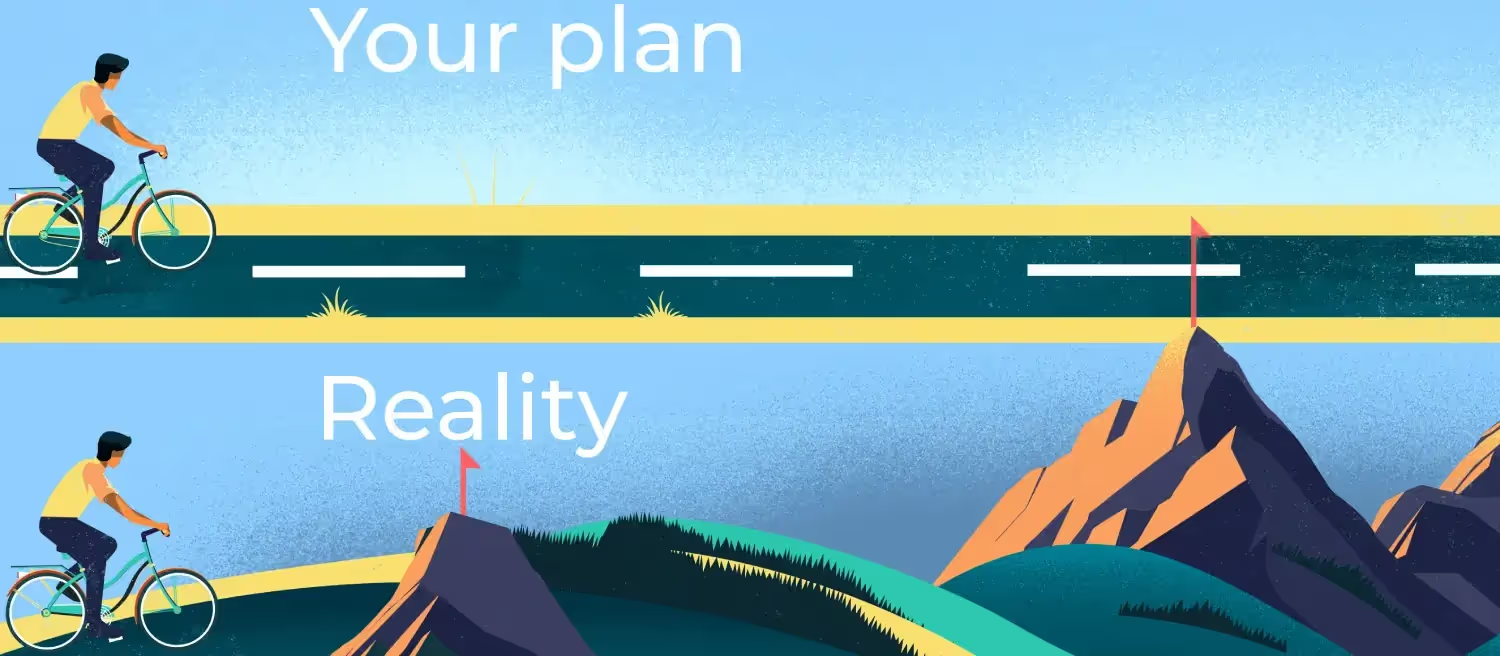
Technology is wonderful. Enterprise software such as ERPs, MRPs, and other supply chain management platforms collect enormous amounts of data and effectively automate a wide array of tasks and processes to save industrial planners precious time.
However, it's not uncommon for ERP and MRP systems to go overboard and generate a constant flux of "exception messages" — simply because they're not designed to cope with a volatile reality.
Without a way to make sense of that flood of automatic notifications and identify which should be prioritized, it's only too easy for Supply Chain and Manufacturing managers to drown in the mass.
When Exceptions Become The Rule
"Stock fell below safety stock level." "Coverage not provided by master plan". "Order proposal has been changed". As a Supply Chain or Manufacturing manager working with ERP and MRP systems, you're probably somewhat familiar with such "exception messages." The system issues Exception messages whenever reality deviates from the plan. In other words, it's a way for the ERP to alert you to unforeseen events and issues (such as stock shortage or excess, procurement blockers, timeline inconsistencies, and so forth).
This is a good thing, right? You get instant notifications in case of problems, enabling you to analyze and solve them on time and stay on top of your inventory and schedule while maximizing operational performance.
The trouble is that the typical industrial planner receives hundreds or even thousands of such messages daily. That's a lot and definitively more than one can absorb. The exception messages usually don't provide insights into the operational and financial impact of the issues. This means it's up to you to decide which to prioritize based on the information you have… and sometimes just on a hunch.
Moreover, going through an endless list of specific messages about specific items might cause you to over-concentrate on details instead of focusing on the bigger picture. There is such a thing as too much information.
Why Such A Slew Of Exceptions?
Is it normal to buckle under a seemingly never-ending stream of inbound exception messages? The answer is no… and yes. A Gartner research paper, Maverick* Research: ‘Demand-Driven’ Is Deadly to Your Supply Chain analyzes that the industry's overall approach to Supply Chain planning is still essentially driven by demand forecasts. Manufacturers strive to anticipate future product demand as accurately as possible and base their inventory, procurement, as well as production plans on these estimates. At the same time, this made total sense a few decades ago, when markets and supply chains were significantly simpler and stabler; this planning method is arguably less efficient in a world in constant flux. With the acceleration of product life cycles, the impetus for diversification, and the overall fragility of global supply chains, formulating accurate forecasts is increasingly challenging. As a result, it becomes impractical to base all supply and operations plans on demand estimates — however, this is still the philosophy behind industry-grade ERP and MRP systems.
In sum, exception messages multiply due to the growing hiatus between a prediction-based approach to industrial planning and an increasingly unpredictable world.
A Necessary Evil?
Achieving flawless forecasting reliability is hardly an option in our changing world. As it is impossible to eliminate uncertainty in operations altogether, exception messages might have to be viewed as a fact of life.
Is there a surefire way to tweak the industrial planning process to optimize these messages' intake, prioritization, and overall management? Not really, unless you have significant time and budget on your hands. Process adjustments tend to be time-consuming and expensive (if only because of the need to engage in change management activities). So are initiatives aiming to reconfigure and customize ERP systems. And so are more recent attempts at using generic low-code and no-code platforms to build applications for managing exception messages automatically. Otherwise, taking special training can help you to navigate the lists of messages faster and more efficiently — to some extent.
Fortunately, there's another way to improve the handling of Supply Chain and Production anomalies without upending the whole process and system.
How Advanced Data Science Is Changing The Game
The key reason why Supply Chain and Manufacturing managers find themselves at a loss when faced with their never-ending lists of exception messages is a lack of information about each message's real meaning and impact.
How can you tell the inconsequential from the critical among the spate of potential and actual issues reported by the system? How can you identify which exception message will most impact sales orders, cycle times, and other KPIs? Figuring this out manually is next to impossible in our modern, complex factories that involve many moving parts. Excel and other such office tools don't help much.
However, what if you had data intelligence tools providing meaningful data and insights to help you analyze, prioritize, and tackle supply chain anomalies and discrepancies?
Exception messages may inform you that parts are missing. But what if you had a system letting you know that a specific missing part would jeopardize the delivery of a costly end product to a strategic customer?
That's just what factory operations management platforms such as Pelico's are making possible. Acting as intelligent layers that sit on top of transactional systems (ERPs, PLMs, Time Tracking…), such software consolidate all the information at the plant level to provide a comprehensive, real-time view of supply, demand, and operations, with smart analysis capabilities to make sense out of the data and offer recommendations for prioritization.
The teams can anticipate production and supply chain bottlenecks, and they have the necessary intelligence to support their decision-making. As a result, they focus on actual issues rather than on exception messages. In a nutshell, they are empowered to build and operate tomorrow's resilient, adaptable supply chains.
Interested in Operational Intelligence? Schedule a fifteen-minute call with our experts to see Pelico in action.