4 ways AI revolutionises complex industrial operations, but is it the only approach for the future digital industry?
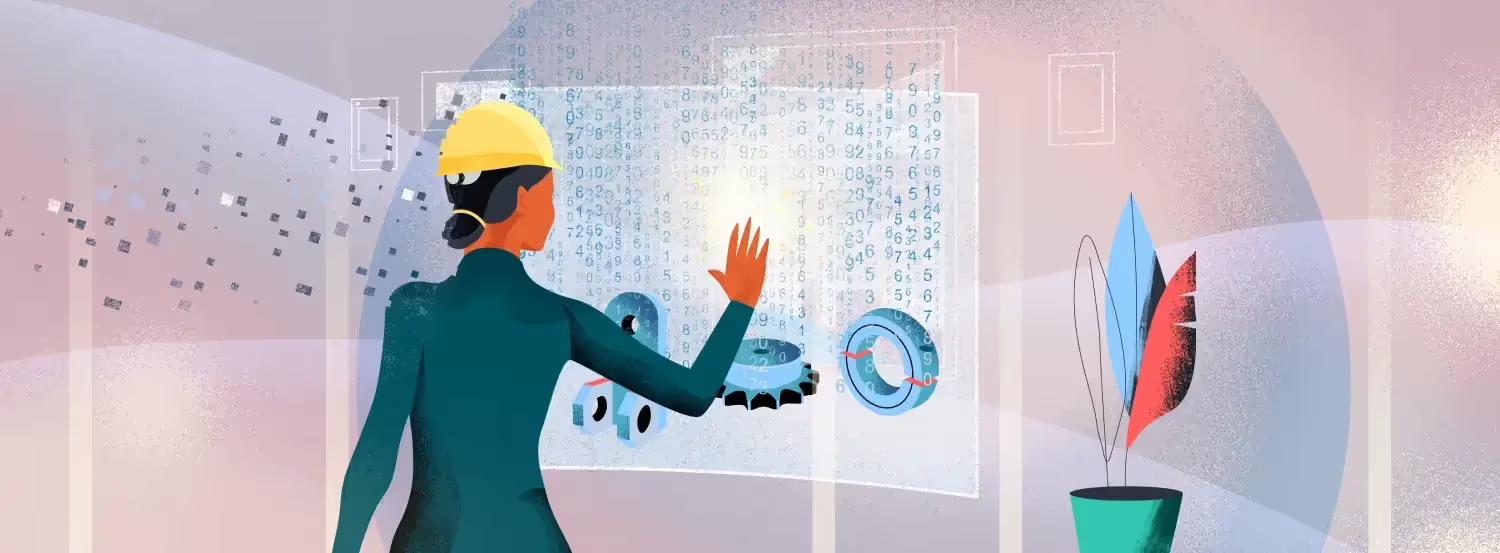
Manufacturing becomes more complex every year. Yet productivity growth for many industrial companies has been shrinking. All the while, the volatility that characterizes our times continues to demand ever greater variety and adaptability from manufacturers.
Today, most industrial operations involve many steps, parts, and teams. But complex operations include the logistical challenges of proliferating parts, each with its own multi-stage, technologically complex processes, interactions, and dependencies. They also might require different raw materials, along with separate operational expertise, in turn creating organizational intricacy.
In short, every dimension of the complex operation becomes more challenging and less robust than that of the simple manufacturer’s shop floor. Overseeing such things can be arduous and prone to maddening complications and setbacks. And it is precisely in areas like this that artificial intelligence (AI) can usher in a new era for manufacturing. At the same time, for certain challenges, other technologies provide excellent results
Life before AI
Even prior to the pandemic, manufacturing had its share of problems: 20% of every dollar spent in the industry is wasted. Given the share of global GDP this represents, the sheer scale of loss is shameful.
Variable demand, expectations about product customizability, and shorter product cycles are factors putting pressure on organizations. Indeed, today’s volatile business environment can make profits elusive. The hypercompetitive nature of the industry means that any small stumble can scorch a manufacturer’s bottom line. According to Rand Group, 98% of enterprises said a single hour of operational downtime costs their business a minimum of $100,000. For many of them, the expense is better counted in the millions.
The more complex the industrial operation, the greater the risk of asymmetrical information between different teams wreaking havoc on operational planning. This is exactly where AI can deliver some of its most significant advantages.
With the increasing complexity of industrial operations, the need to predict outcomes and to adapt to unexpected changes is becoming more acute as well. This is another instance where AI can provide support for human decision-making.
What is AI capable of?
Artificial intelligence can process terabytes of data emanating from sensors, machines, and people that no human could possibly analyze. By implementing machine and deep learning models, and enabling automation in their operations, manufacturers can observe patterns and predict the impact of a single variable within a complex system.
This has enormous cost-saving potential. But concretely, how can AI help with complex industrial operations on a daily basis?
Planning: by providing a list of recommended actions for minor emergencies, AI can guarantee that teams are prepared to respond as autonomously as possible to unplanned circumstances. The French multinational Danone, for example, began using machine learning to predict demand variability and planning. The initiative has produced a 20% reduction in forecast error, a 30% reduction in both lost sales and product obsolescence, and no less significantly, a 50% reduction in demand planners’ workload.
Agility: with the right integration of AI within R&D processes, manufacturers can increase the speed at which they generate, develop, and get new products to their customers. This offers a decisive competitive advantage in terms of agility, allowing companies to adapt to the novel demands of the business environment more rapidly.
For example, Intel has developed AI platforms for optimizing the product validation process for microchips, lowering costs and shortening time to market. One of these platforms, CLIFF, creates new tests for hard-to-validate functionalities to discover hidden bugs as quickly as possible, performing 230 times better than standard regression tests.
Raw material costs: AI can assist manufacturers by analyzing market conditions and extrapolating likely price changes and impacts. This helps to improve predictions of raw material costs, which can be difficult to foresee. Predicting shortages of one material better reduces possible waste elsewhere, offering planners earlier opportunities to make adaptations to production schedules. This prevents purchases of related in-supply raw materials that would otherwise be rendered useless.
Productivity: manufacturing processes themselves can even be streamlined by applying AI to assembly line programming. For example, Mitsubishi Electric is exploring applications of AI in automatically and adaptively adjusting the rate, speed, and acceleration of industrial robots. With this decision, Takt time was reduced to one-tenth of conventional approaches, improving throughput.
But where might AI not be needed?
AI is a powerful tool that is revolutionizing many areas of industrial operations. However, at least for now, machine learning — the most famous AI technique — requires time and often truly vast amounts of data. At times, this may be simply unavailable or uneconomical to collect. Moreover, for certain use cases, AI is not actually the optimum solution; other faster algorithms can help manage complexity more efficiently.
Communication: to meet ambitious production and quality goals, effective communication is essential. Siloed and scattered data between functions is a driver of error. A common view of operations, thanks to vertically integrated data management solutions, is one way that teams can achieve greater transparency. This, in turn, allows them to anticipate production blockers and avoid problems.
A shared framework removes the risk of data asymmetry, offering a common reference point for communication. With different teams all working from a single source of truth, operational complexity becomes more manageable and output foreseeable, without any need to turn to machine learning.
Accelerated collaboration: teams supported by algorithmic planning can be empowered to collaboratively simulate alternative production scenarios and create communication channels across different functions. Again, hefty machine learning is not always needed here. The right digital solutions can make this a simple process, taking out the heavy lifting from simulations and leveraging advanced analytics to offer what-if outcomes, all under short turnaround times.
Efficiency and agility: if information is widely shared across functions, teams can better estimate how to prioritize solutions, and which to take according to their impact on performance. This has benefits for compliance with planning, compliance with deadlines, improvements in sales forecasting, and much more. Moreover, non-AI solutions are available that can automate these processes, going as far as offering action plans weighing tasks by level of priority. Combining this functionality with the simulation capabilities makes the teams agile and able to respond to unexpected events. Teams can take decisions with greater efficiency in volatile environments, minimizing the impact of disruptions on overall performance.
Production teams need a solution that consolidates all localized intelligence to provide a cross-team, cross-domain view. They need smart capabilities to make sense out of data, to pinpoint and flag issues — both actual and potential. They also need a platform enabling collaborative problem-solving in order to bring everyone around the optimal solution.
It is important to select, and invest in, the right tool for the job. For some of these tasks, AI is the perfect instrument. For others, faster digital solutions can provide more immediate value. It is easy to be swept up by trends in technology, but smart decision making around when AI is and is not needed has the potential to be a modern-day business differentiator. Cutting-edge machine learning can be a costly and time-consuming remedy. Nevertheless, with the right investment, time, and data — it can be a source of remarkable value.